نوشته دکتر محمدرضا عاطفی

مشاور استراتژی و آینده پژوه
عضو هیات علمی دانشگاه
ابزارها و تکنیکهای تولید ناب
بخش دوم
۸- اثربخشی کلی تجهیزات
Overall Equipment Effectiveness (OEE)
اثربخشی کلی تجهیزات چیست؟
اثربخشی کلی تجهیزات یک معیار کلیدی محبوب است که برای کمک به مدیریت فرآیندهای تولید مبتنی بر تجهیزات استفاده میشود. OEE بهرهوری یک سیستم را پایش میکند تا ببیند یک فرآیند چقدر در دسترس است، چقدر سریع است و کیفیت آن در ساخت قطعات غیر معیوب چقدر است.
OEE سیستمی است که برای اندازهگیری بهرهوری تولید استفاده میشود. درصد زمانی را که واقعاً صرف تولید شده است را اندازهگیری میکند.OEE چارچوبی برای اندازهگیری بهرهوری یک فرآیند تولید است. سه دسته از عوامل پایش میشود:
- در دسترس بودن (به عنوان مثال، خرابی)
- عملکرد (به عنوان مثال، عملیات آهسته)
- کیفیت (مثلاً عیوب)
چگونه اثربخشی کلی تجهیزات کمک میکند؟
OEE یک معیا و سنجشی برای ردیابی اقدامات حذف اتلافها از فرآیند تولید فراهم میکند. OEE=100% به معنای تولید کامل است (تولید فقط قطعات خوب، در سریعترین زمان ممکن، بدون توقف).
هدف OEE
با اندازهگیری بهرهوری بر حسب زمان، تولیدکنندگان میتوانند بینشی در مورد چگونگی بهبود عملکرد کلی تولید به دست آورند. این سیستم به شناسایی ضایعات، پایش بهبود و ارتقای کارایی تجهیزات ساخت کمک میکند.
کیفیت، عملکرد و در دسترس بودن واقعاً به چه معناست؟
- کیفیت تعداد عیوب را میسنجد. نمره 100% نشان میدهد که ایرادات صفر است.
- عملکرد، چرخههای کند یا سرعتی کمتر از زمان استاندارد را اندازهگیری میکند. امتیاز 100٪ نشان میدهد که همه چیز در سریع ترین زمان ممکن اجرا میشود.
- در دسترس بودن هر توقفی را در نظر میگیرد. امتیاز 100% نشان میدهد که فرآیند همیشه در زمانهای تولید تعیین شده در حال تولید بوده و توقفات برنامهریزی نشده نداشته است.
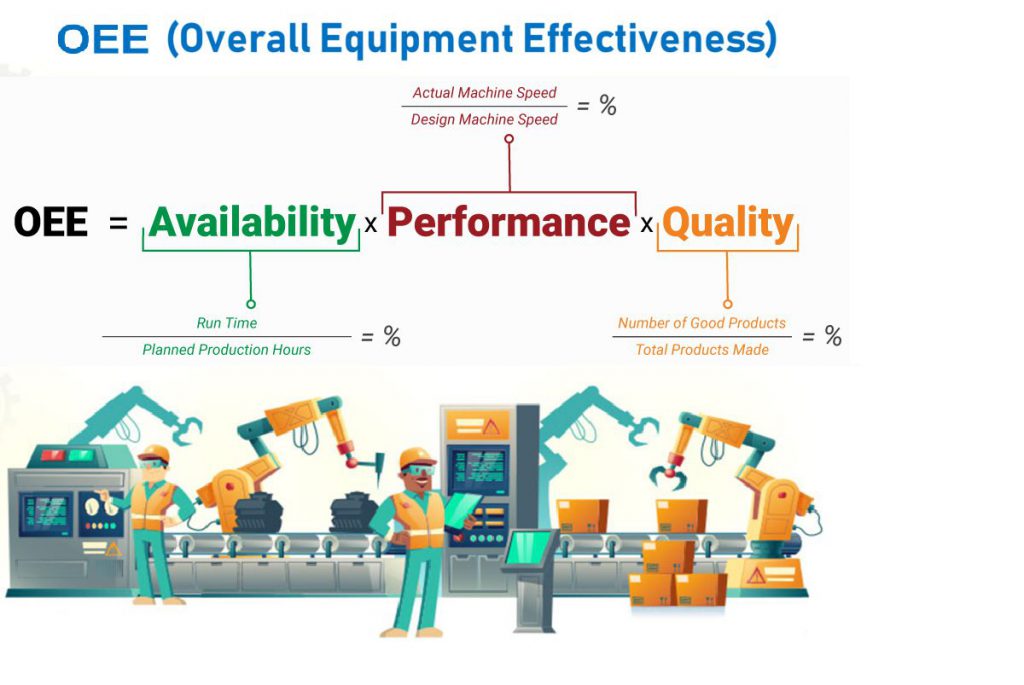
۹- جیدوکا (خودمختاری) Autonomation or Jidoka
جیدوکا چیست؟
مفهوم جیدوکا زمانی توسعه یافت که ساکیچو تویودا، بنیانگذار گروه تویوتا، یک ماشین بافندگی خودکار را اختراع کرد که با پارگی نخ بهطور خودکار متوقف میشد. در این حالت شاتلهای تقریباً خالی را بهسرعت بیرون میآورد و بلافاصله یک شاتل جدید را وارد میکرد. این اختراع اپراتورها را قادر میساخت تا به جای نظارت بر دستگاههای بافندگی، کارهای ارزشآفرین بیشتری انجام دهند. ایده طراحی ماشینآلاتی که در صورت بروز مسائل بهطور خودکار متوقف میشوند، در نهایت به بخش مهمی از هر فرآیند تویوتا تبدیل شد.
Autonomation (ادغام اتوماسیون و خودمختار) اساساً اتوماسیون با عنصر انسانی است. انسان را از دست ماشین رها میکند زیرا اگر ماشین خودش متوقف شود دیگر نیازی به نظارت دائمی انسان ندارد.
جیدوکا این ایده است که سازندگان باید تجهیزاتی را طراحی کنند تا به طور جزئی فرآیند تولید خودکار شود (اتوماسیون جزئی معمولاً بسیار ارزانتر از اتوماسیون کامل است) و به طور خودکار هنگام شناسایی نقص متوقف شود.
این ابزار به طور مستقیم با کنترل کیفیت مرتبط است و به اپراتور انسانی اجازه میدهد تا فرآیندهای خودکار را به محض مشاهده خرابی متوقف کند.
بنابراین جیدوکا با آموزش صحیح اپراتورها نیاز به تعداد زیادی بازرس کیفی را کاهش میدهد و بخشی از این وظیفه را به خود اپراتور محول میکند.
جیدوکا چگونه کمک میکند؟
پس از جیدوکا، کارگران میتوانند به طور مستمر چند ایستگاه کاری (کاهش هزینههای نیروی کار) را نظارت کنند و بسیاری از مسائل کیفیت را میتوان بلافاصله شناسایی کرد (بهبود کیفیت).
اصول جیدوکا
- یک ناهنجاری یا مسئله را کشف کنید.
- روند عملیات را متوقف کنید.
- مسئله موجود را برطرف کنید.
- برای جلوگیری از مسائل بعدی، علت اصلی را کشف کنید.
نوآوری اولیه و اصلی جیدوکا این است که مسائل احتمالی و پتانسیلهای بروز خطا در مراحل اولیه شکل گیری و در حین فرآیند شناسایی میشود و نه در پایان فرآیند تولید. بازرسی در طول فرآیند تولید میتواند نقش کلیدی در جلوگیری از بروز عیب در مراحل بعدی ایفا میکند.
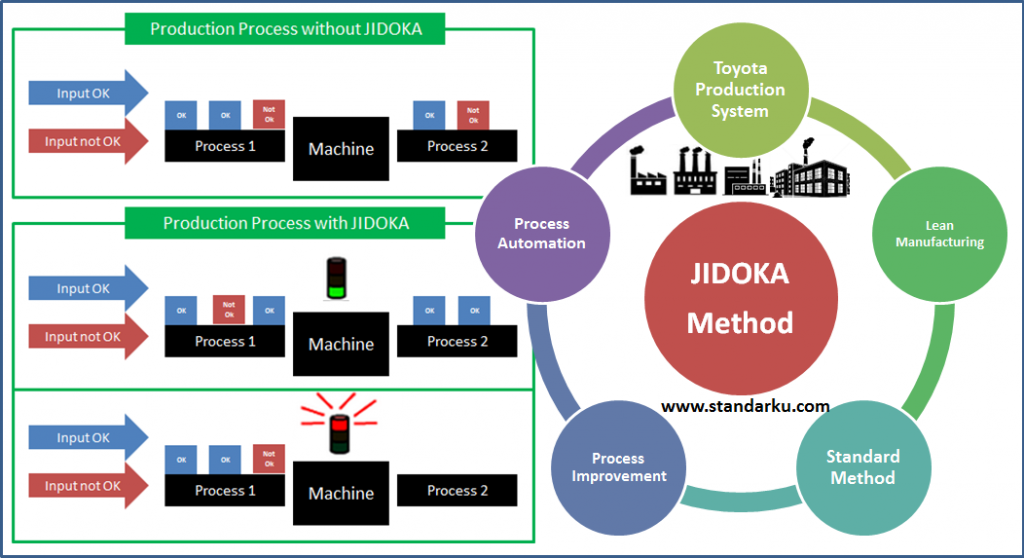
۱۰- چراغها و تابلوهای آندن Andon
آندن چیست؟
آندن سیستمی است که مدیریت را از یک مسئله کیفی یا فرآیند مطلع میکند. این اغلب با استفاده از یک طیف نور یا سایر سیگنالهای ویدیویی یا صوتی که مدیریت نقص، کمبود یا سایر مسائل را هشدار میدهد، انجام میشود.
یک سیستم بازخورد بصری برای کف کارخانه است که وضعیت تولید را نشان میدهد، در صورت بروز یک اشکال یا نیاز به کمک، هشدار میدهد و اپراتورها را قادر میسازد تا فرآیند تولید را متوقف کنند.
چگونه استفاده میشود؟
در تولید، چراغهای آندن به طور کلی در خطوط مونتاژ استفاده میشود. چراغهای رنگی مختلف برای نشان دادن مسائل مختلف و اقدامات مورد نیاز استفاده میشود. اپراتورها ممکن است یک آندن را روشن کنند تا علامت دهند که در خط مونتاژ مسئلهای وجود دارد. در یک محیط اداری، یک نور قرمز رنگ (آندن) ممکن است نشان دهنده خرابی دستگاه فکس یا چاپگر باشد.
در خودروها، چراغهای هشدار روی داشبورد خودرو نمونههایی از آندن هستند. آندنها زمانی بهترین عملکرد را دارند که بسیار قابل مشاهده و قابل درک باشند. بنابراین، به عنوان مثال، یک چراغ هشدار آندن روی خودرویی که سیگنال کم بنزین را نشان میدهد، نشان دهنده یک عمل واضح است: باک را با بنزین پر کنید.
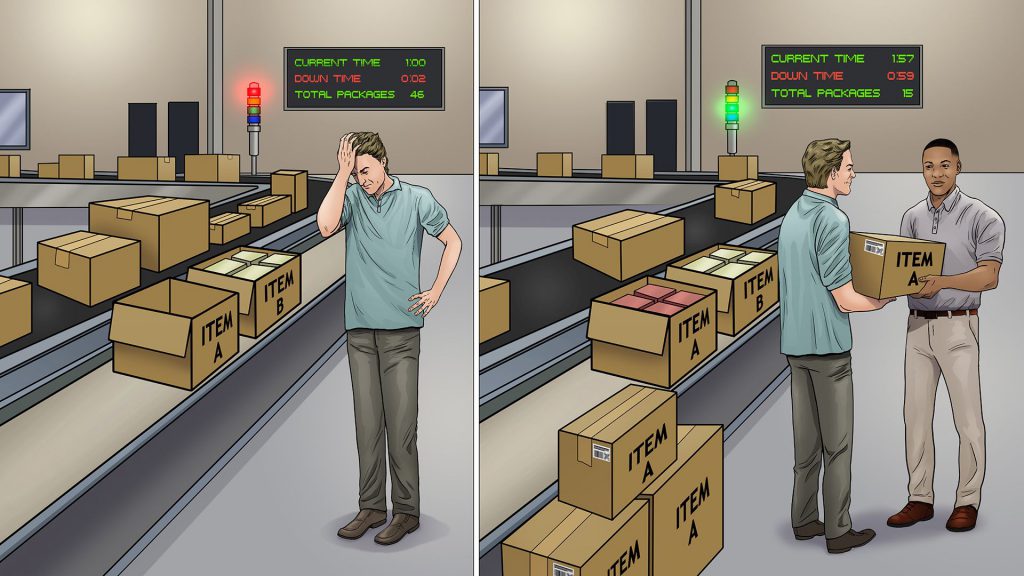
۱۱- تجزیه و تحلیل گلوگاه Bottleneck Analysis
تحلیل گلوگاه چیست؟
تولید ناب اغلب از تحلیلهای گلوگاه برای تعیین کُندترین فرآیندها و مراحل در جریان تولید استفاده میکند. سرعت بخشیدن به تنها یک یا دو بخش اغلب میتواند به طور چشمگیری کل فرآیند تولید را سرعت بخشد.
گلوگاه (یا محدودیت) در زنجیره تامین به منبعی اشاره دارد که بیشترین زمان را در عملیات میبرد. برای مثال، هنگام پیادهروی، گلوگاه به کُندترین عضو یک گروه پیادهروی اشاره دارد. آن عضو میتواند سرعت کل گروه را تعیین کند. همین امر در مورد فرآیندهای تولید نیز صدق میکند. اگر بخشی از یک زنجیره تامین به طور غیر ضروری کُند باشد، میتواند سرعت و کارایی کل فرآیند تولید را کاهش دهد.
تجزیه و تحلیل گلوگاه مشخص میکند که کدام بخش از فرآیند تولید، توان عملیاتی کلی را محدود میکند و عملکرد آن بخش از فرآیند را بهبود میبخشد.
چگونه تجزیه و تحلیل گلوگاه کمک میکند؟
تحلیل گلوگاه با تقویت ضعیفترین حلقه در فرآیند تولید، توان عملیاتی را بهبود میبخشد.
هدف از تجزیه و تحلیل گلوگاه
هدف تجزیه و تحلیل گلوگاه تعیین کندترین بخشهای فرآیند تولید و سپس کشف چگونگی سرعت بخشیدن به آنهاست. این فرآیند میتواند پرهزینه باشد، اما معمولاً منجر به افزایش کارایی و سود میشود. نادیده گرفتن یک مسئله گلوگاه میتواند بسیار پرهزینه باشد.
چه زمانی باید تحلیل گلوگاه اجرا شود؟
هنگامی که مدیران یا اپراتورها احساس کنند که فرآیند تولید بیش از حد طولانی شده است. در این مرحله، مدیران تلاش خواهند کرد تا دقیقاً تعیین کنند که گلوگاه در کجا رخ میدهد.
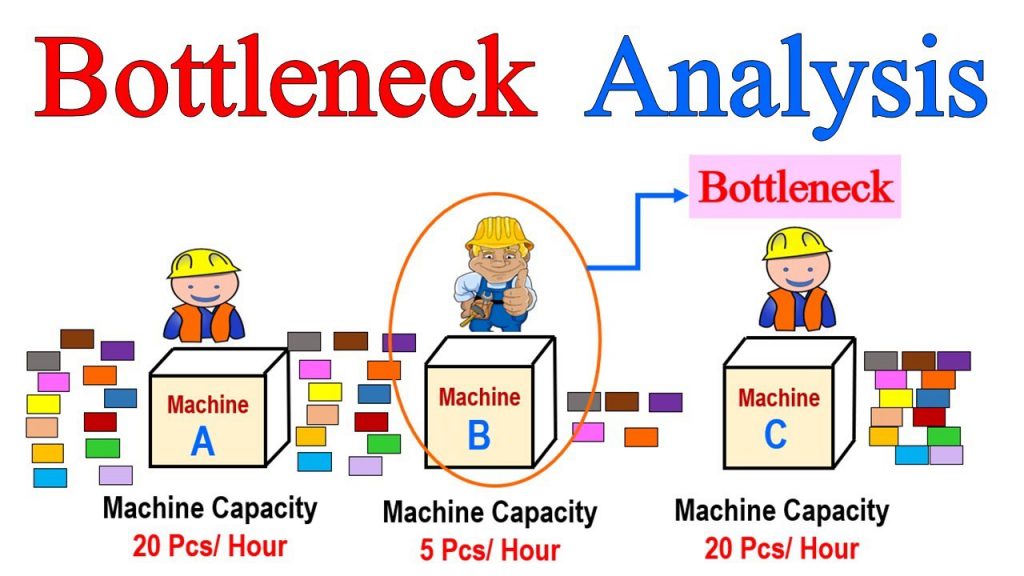
۱۲- جریان پیوسته Continuous Flow
جریان پیوسته چیست؟
جریان پیوسته به معنای تولید و جابجایی یک آیتم در یک زمان (یا یک دسته کوچک و ثابت) برای مطابقت با زمان تکت است. هر قطعه بلافاصله از یک مرحله فرآیند به مرحله بعدی منتقل میشود، بدون هیچ وقت تلف شده (یا هیچ اتلاف دیگری) در این بین.
جریان پیوسته از طریق سیستم فورد توسعه یافته است و شامل مفاهیمی مانند استفاده از قطعات به طور مداوم قابل تعویض است تا زمان چرخه بتواند سازگار باشد. خود خط مونتاژ؛ چیدمان ماشینها به گونهای که قطعات بتوانند به راحتی بین کارها جریان داشته باشند. و اطمینان از اینکه نرخ ساخت قطعات با میزان مصرف قطعات در مونتاژ نهایی مطابقت دارد.
جریان پیوسته مخالف تولید دستهای است و ارتباط نزدیکی با کانبان و تولید درست به موقع دارد. تولید جریان پیوسته شامل تولید تنها یک محصول در یک زمان در هر مرحله از فرآیند است، بر خلاف تولید دستهای که شامل تولید چندین محصول در یک زمان است. این در نگاه اول کارایی کمتری نسبت به تولید دستهای دارد. اما، سطح کار در حین ساخت را به حداقل میرساند و زمان چرخه تولید را کاهش میدهد، زیرا لازم نیست هر محصول قبل از حرکت به مرحله تولید بعدی منتظر دیگران بماند.
هدف جریان پیوسته استفاده از بررسی و بهبود مستمر برای ادغام تمام عناصر تولید است. با هدف گذاری برای فرآیند تولید جریان مداوم، استلاف و سایر مسائل هویدا میشوند و سپس قابل حل هستند. در نهایت، بسیاری از اصول و ابزارهای ناب حول ایجاد فرآیند تولید جریان پیوسته متمرکز هستند.
فرآیند جریان مداوم معمولاً شامل یک کارخانه است که 24 ساعته بدون وقفه و با اتلاف کمی کار میکند. مناطقی مانند پالایش نفت، ذوب فلزات و فرآوری گاز طبیعی برای فرآیند جریان پیوسته ایده آل هستند.
جریان پیوسته تولیدی است که در آن کار در فرآیند به آرامی از طریق تولید با حداقل (یا بدون) بافر بین مراحل فرآیند تولید جریان مییابد.
جریان مداوم چگونه کمک میکند؟
جریان مداوم بسیاری از اشکال ضایعات (مانند موجودی، زمان انتظار و حمل و نقل) را حذف میکند.
یک قطعه در جریان تولید One Piece Flow چیست؟
جریان تنها یک محصول یا خدمت در خط تولید یا فرآیند در یک زمان است. جریان یک قطعه در فرآیند برعکس پردازش دستهای است که در آن تعداد زیادی از محصولات به طور همزمان در خط تولید قرار دارند و به صورت دستهای یا گروهی تولید میشوند. در یک قطعه در جراین تولید به جای انتظار، حمل و نقل و ذخیره سازی محصول، تمرکز بر روی ساخت خود محصول است.
مزایای یک قطعه در جریان تولید چیست؟
- توانایی تشخیص زودتر و دقیقتر عیوب
- انعطاف پذیری بیشتر برای سفارشی سازی و برآوردن خواستههای مشتری
- کاهش هزینهها از طریق حذف ضایعات هزینه
- کاهش میزان کار در حال انجام در نتیجه کارآمدتر کردن هر مرحله
- پیش بینی زمان آسانتر حمل و نقل
برای افزایش کارایی، شرکتها میتوانند اجرای One Piece Flow را انتخاب کنند و به سادگی تعداد محصولات تولید شده در یک دسته را کاهش دهند.
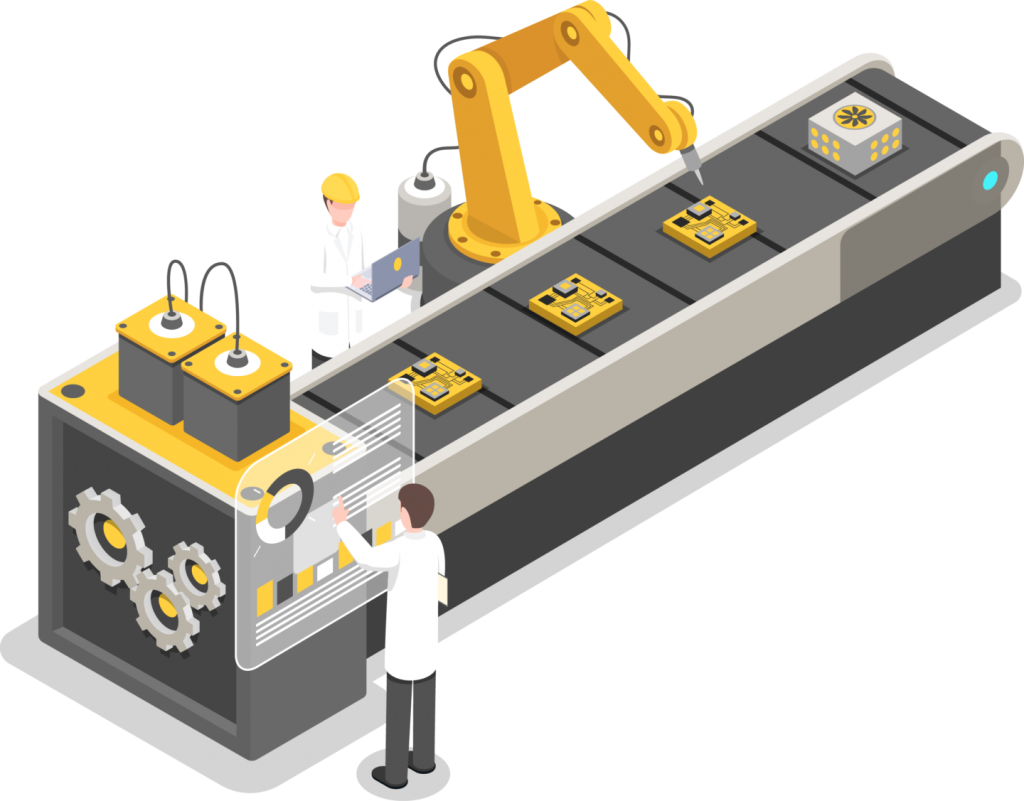
۱۳- گمبا (مکان واقعی)Gemba
گمبا چیست؟
پیادهروی گمبا به عنوان یک گشت و گذار در کف مغازه تعریف میشود. یک اصطلاح ژاپنی است که به عنوان “مکان واقعی” تعریف میشود. در تجارت، به حوزهای اطلاق میشود که در آن ارزش واقعی ایجاد میشود. در تولید به کف کارخانه اشاره دارد. همچنین میتواند محل ساخت و ساز، مکان فروش و غیره باشد. بازدید یک مدیر از محل کار است. ایده گمبا در تولید ناب این است که مدیریت باید برای جستجو و رفع مسائل قابل مشاهده به کف کارخانه برود. گمبا استدلال میکند که مسائل تولید را نمیتوان از طریق یک واحد حل کرد. آنها نیاز به حضور فیزیکی واقعی توسط حل کنندههای مسئله در کف کارخانه دارند. فلسفهای است که به ما یادآوری میکند که از دفاتر خود خارج شویم و زمان خود را در کف کارخانه بگذرانیم – مکانی که اتفاقات واقعی در آنجا رخ میدهد.
گمبا چگونه کمک میکند؟
گمبا درک عمیق و کاملی از مسائل تولید در دنیای واقعی را ترویج میکند – با مشاهده دست اول و با صحبت با کارمندان کارخانه.
گمبا چگونه پیاده سازی میشود؟
گمبا یک فرآیند گام به گام است:
- مهندسان به طور فیزیکی به طبقه تولید میروند تا فرآیندها را مشاهده کنند.
- مهندسان دادهها را جمع آوری میکنند و کار انجام شده را درک میکنند
- مهندسان سوال میپرسند.
- مهندسان در مورد مسائل یاد میگیرند و راه حلهایی ارائه میدهند.
Gemba Walks اشاره به کارکنانی دارد که در کارخانه وقت میگذارند، بررسی میکنند که چه اتفاقی میافتد و تعیین میکنند که آیا مسئلهای وجود دارد یا خیر. در فلسفه مدیریت ناب، از کارکنان انتظار میرود حداقل یک بار در هفته پیادهروی گمبا انجام دهند.
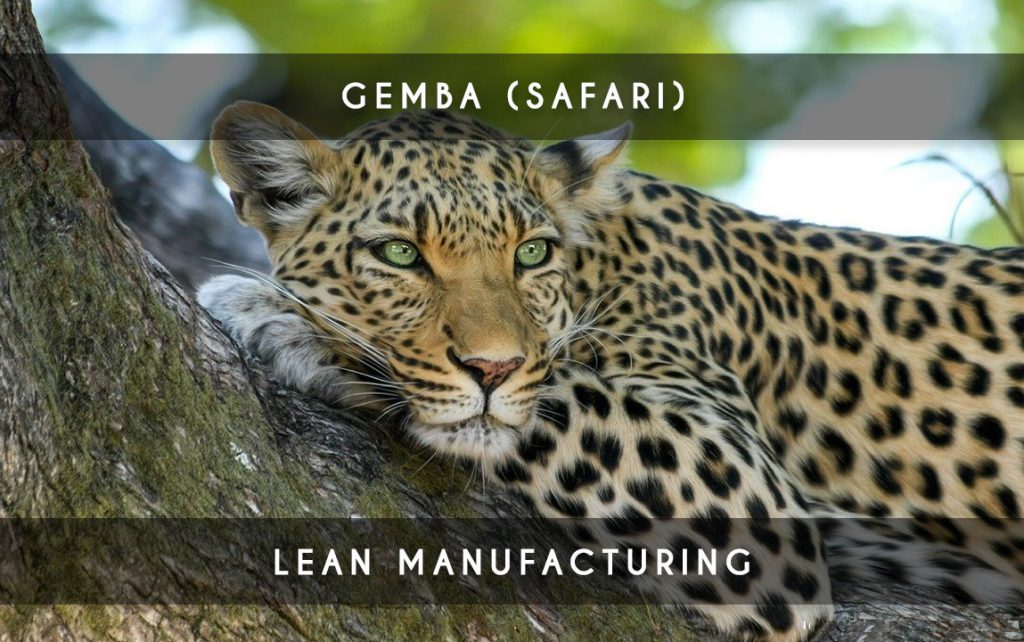
۱۴- زمان تکت Takt Time
زمان تکت چیست؟
تکت تایم از کلمه آلمانی به معنای “نبض یا آهنگ” گرفته شده است. زمان تکت به طور دقیق یک روش نیست. این عنصر اندازهگیری ضروری روش تولید جریان پیوسته است. این نرخ تولید هر محصول است که باید از نظر تئوری با نرخ فروش یکسان باشد.
زمان تکت به این اشاره دارد که هر چند وقت یکبار یک قطعه یا محصول باید تولید شود تا نیازهای مشتری را بر اساس میزان فروش برآورده کند. زمان تکت با تقسیم زمان کار موجود در هر شیفت(روز/ماه/سال) بر میزان تقاضای مشتری در هر شیفت(روز/ماه/سال) محاسبه میشود. پس زمان تکت سرعت تولید است (مثلاً تولید یک قطعه در هر 34 ثانیه) تولید را با تقاضای مشتری همسو میکند. تولید در زمان تکت به این معنی است که یک سیستم تولیدی قادر است به سرعت به مسائل پاسخ دهد، علل خرابی برنامهریزی نشده را حذف کند و زمان تغییر خط تولید برای یک محصول دیگر را کاهش دهد.
در حالت ایده آل، اگر تمام مراحل تولید به خوبی هموار باشند (طبق روش هیجونکا)، هر قطعه در مدت زمانی برابر با زمان تکت باید تولید شود.
هدف تکت تایم این است که زمان مصرف شده در تولید را تابعی از تقاضای واقعی بازار تعریف کند. با همسو کردن تولید با تقاضا، یک ریتم ایدهآل وجود دارد که به نام «سیستم کششی» نیز شناخته میشود، یعنی نیاز بازار به «کشش» تولید، نه برعکس. زمان تکت برای اطمینان از جریان مداوم و استفاده کامل از منابع موجود، ریتمی را در سراسر زنجیره تامین ایجاد میکند.
زمان تکت چگونه کمک میکند؟
زمان تکت یک روش ساده، سازگار و شهودی برای تولید سرعت ارائه میدهد. زمان تکت یک هدف کارایی برای کف کارخانه (قطعات واقعی / قطعات هدف) است.
هدف زمان تکت
هدف زمان تکت ارائه محصول مناسب به مشتری مناسب در زمان مناسب است. این تضمین میکند که محصولات به کارآمدترین روشی تولید شوند، که تقاضای مصرف کنندگان را برآورده کنند.
یکی دیگر از اهداف زمان تکت ایجاد یک جریان قوی از عملیات در یک زنجیره تامین است. اندازهگیری زمان تکت به مدیران این امکان را میدهد تا ظرفیت و مسائل مربوط به هموارسازی را در یک زنجیره تامین تعیین کنند و سپس راهحلهای مناسب را بیابند.
مثال
به عنوان مثال:
زمان کل: 8 ساعت × ۶۰ دقیقه = 480 دقیقه
زمان استراحت: 50 دقیقه
زمان در دسترس: 430 دقیقه
تقاضای مشتری در 8 ساعت: 100 عدد
زمان تکت: ۱۰۰ / ۴۳۰ = 4.3 دقیقه = 258 ثانیه
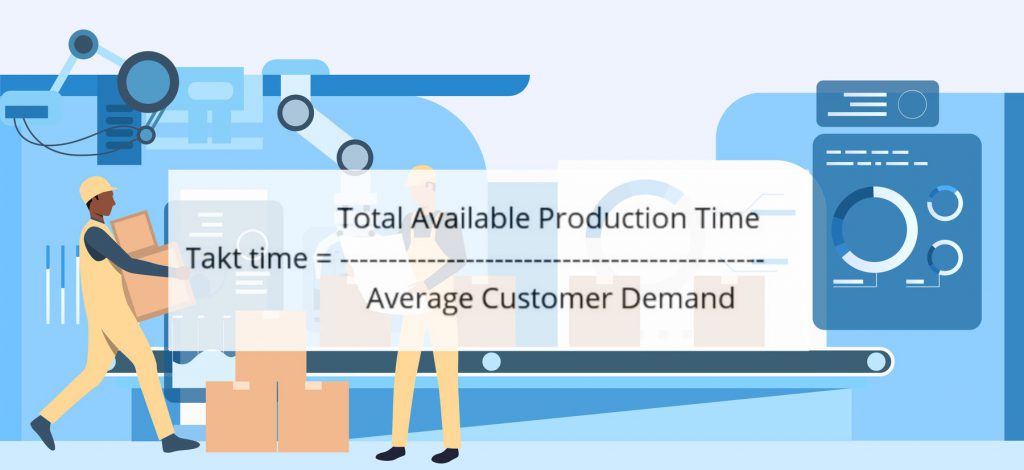
۱۵- نقشهبرداری جریان ارزش Value Stream Mapping
نقشهبرداری جریان ارزش چیست؟
نقشه برداری جریان ارزش یک ابزار تحلیلی است که به روشی ترکیبی اقدام به شناسایی و به تصویر کشیدن تمام جریانهای فیزیکی و اطلاعاتی یک فرآیند میکند.
نگاشت جریان ارزش ابزاری است که برای ترسیم بصری جریان تولید استفاده میشود. وضعیت فعلی و آینده فرآیندها را به گونهای نشان میدهد که فرصتهای بهبود را برجسته میکند. نقشهکشی یک ابزار ناب است که از نمودار جریان برای به تصویر کشیدن هر مرحله از یک فرآیند استفاده میکند.
با نگاشت بصری روابط همه اقلام در یک فرآیند، شناسایی مسائل و اتلافهای احتمالی (زمان تلف شده، منابع یا مواد) آسانتر است. راه حلهای بالقوه روشن میشوند. همانطور که این فرآیند ادامه دارد، راهحلها به صورت بصری به گونهای نمایش داده میشوند که به همه طرفها اجازه میدهد تاثیر یا تغییر فرآیند اصلی را درک کنند. سپس یک تغییر فرآیند در کل سیستم میتواند بسیار موثرتر اجرا شود. از طریق چرخه حیات VSM، تمام فرآیندهای جدید توسط یک نقشه بصری به روز شده نشان داده میشوند، که اجازه میدهد روند بهبود ادامه یابد. از آنجایی که این ابزار ناب از بهبودهای مستمر پشتیبانی میکند، میتوان از آن برای پشتیبانی از کایزن استفاده کرد.
نقشهبرداری جریان ارزش چگونه کمک میکند؟
نقشهبرداری جریان ارزش، اتلافها را در فرآیندهای فعلی نشان میدهد و یک نقشه راه برای بهبود در وضعیت آینده ارائه میکند.
اهداف نقشه برداری جریان فرآیند
نقشهبرداری جریان ارزش سه هدف اصلی را دنبال میکند:
- اتلافها را شناسایی کنید.
- زمان تولید را کاهش دهید.
- کل فرآیند تولید را کارآمدتر کنید.
کاربرد نقشهبرداری جریان ارزش
نقشهبرداری جریان ارزش تقریباً در هر صنعتی قابل اجرا است، اما عمدتاً برای:
- لجستیک،
- زنجیره تأمین،
- توسعه محصول و
- فرآیندهای پشتیبانی و اداری
استفاده میشود.
دادههای مورد نیاز برای تهیه نقشه جریان ارزش
برخی از نقاط داده برای جمع آوری برای نقشه برداری جریان ارزش عبارتند از:
- موجودی
- تعداد اپراتورها
- تعداد شیفتهای کار شده
- اندازه دسته.
- زمان لازم برای ساخت یک محصول
- زمان تغییر خط تولید از یک محصول به محصول دیگر
- زمان در دسترس کاری برای کارخانه
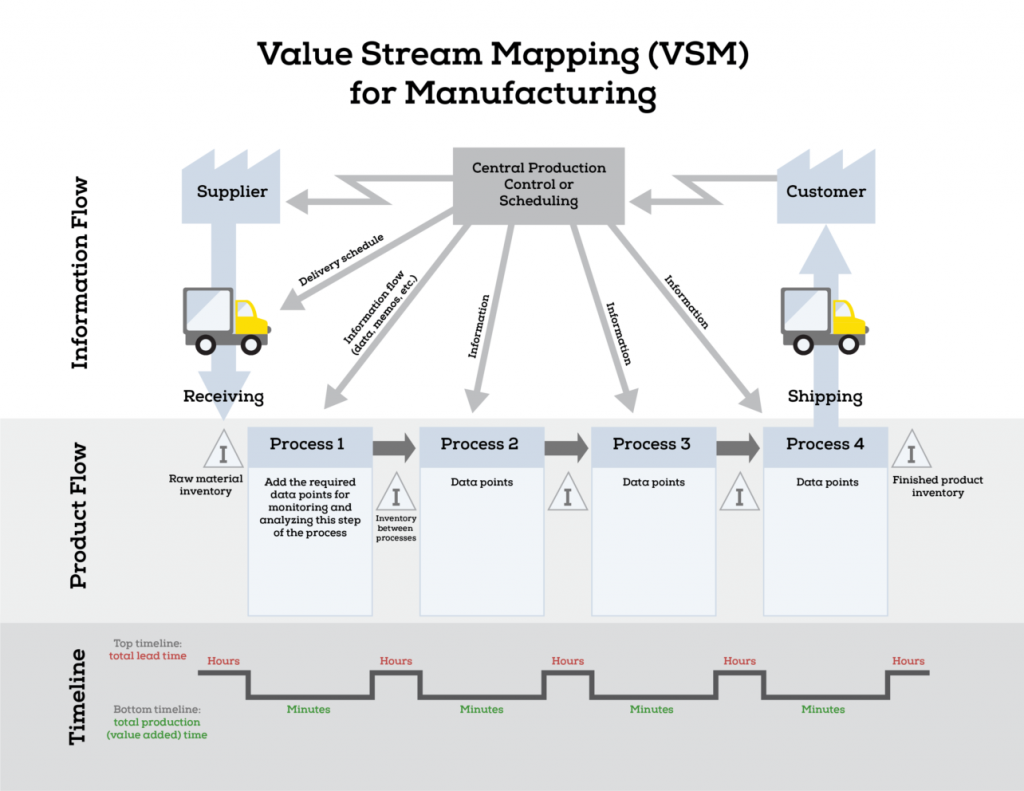
۱۶- تحلیل علل ریشهای Root Cause Analysis
تحلیل علت ریشهای چیست؟
تحلیل علت ریشهای یک روش حل مسئله ناب است که هدف آن دستیابی به ریشه یک مسئله است. فلسفه آن بر این ایده استوار است که بهتر است علت اصلی یک مسئله را درمان کنیم، نه علائم آشکار آن را. تحلیل علت ریشهای به جای اعمال راه حلهای سریع که فقط علائم فوری مسئله را درمان میکند، بر حل مسئله اساسی تمرکز دارد. روشهای مورد استفاده در تحلیل علل ریشهای شامل نمودار استخوان ماهی (نمودار ایشیکاوا) و 5 چرا میباشد.
چگونه تجزیه و تحلیل علت ریشهای کمک میکند؟
تجزیه و تحلیل علت ریشهای کمک میکند تا با اعمال اقدامات اصلاحی برای “علت اصلی” مسئله، مطمئن شویم که یک مسئله واقعاً حذف شده است.
اصول تحلیل علت ریشهای چیست؟
اصول تحلیل علت ریشهای عبارتند از:
- هدف از تجزیه و تحلیل علت ریشهای شناسایی علت اصلی یک مسئله به منظور جلوگیری از تکرار آن است. این یک راهحل بلند مدت است.
- تجزیه و تحلیل علت ریشهای باید یک فرآیند تحقیقی و سیستماتیک باشد تا به طور موثر کار کند.
- هر مسئله معمولاً فقط یک علت ریشهای دارد.
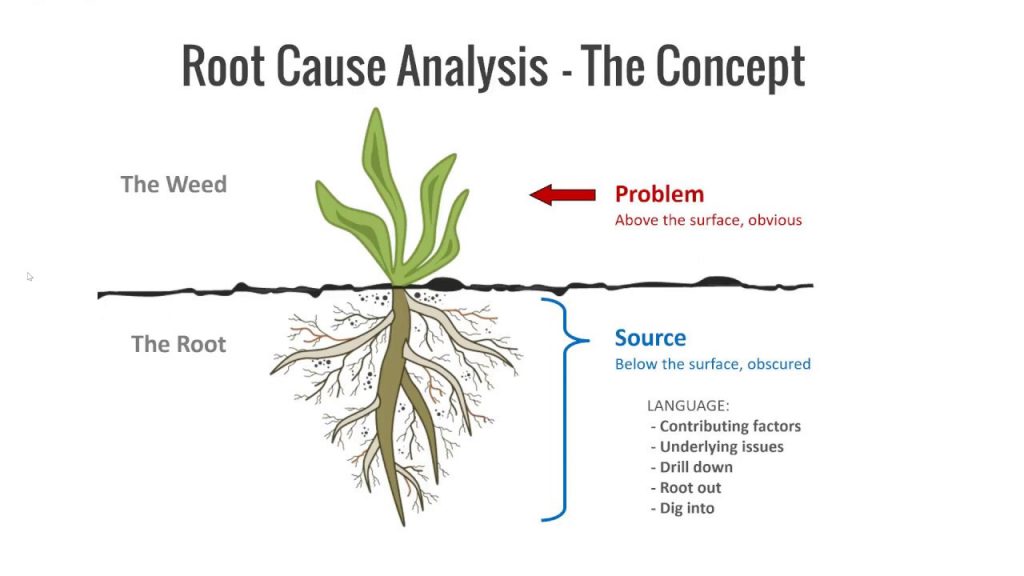
۱۷- پنج چرا
پنج چرا چیست؟
پنج چرا یک روش ناب است که برای تعیین علت اصلی یک مسئله استفاده میشود. مدیران سوال “چرا؟” را تکرار میکنند. و هر پاسخ مبنایی برای سوال بعدی است. این روند تا رسیدن به نتیجه ادامه دارد. تکنیک 5 چرا توسط ساکیچی تویودا توسعه داده شد و تویوتا برای بهبود فرآیندهای تولید خود از آن استفاده کرد. تکنیک 5 چرا به طور کلی نیاز به پشتکار و اراده دارد تا بتواند به طور موثر عمل کند.
هدف این است که در اولین علت یک مسئله متوقف نشویم (اولین چرا) بلکه باید آن را تا زمانی که علت یا علل اصلی شناسایی شود، تجزیه و تحلیل کنیم. این در واقع بیشتر یک اصل است تا یک روش تجزیه و تحلیل علت، زیرا نه به اندازه کافی ساختار یافته است و نه «دقیق» (چرا 5 و نه 4، 6؟ علت اصلی ممکن است به خوبی در دومی کشف شود).
اصول 5 چرا
به منظور اجرای صحیح 5 چرا، مدیران باید قوانین مختلفی را رعایت کنند:
- از کاغذ یا تخته سفید استفاده کنید، نه لپ تاپ یا کامپیوتر.
- مسئله را به وضوح تعریف کنید و مطمئن شوید که همه اعضای تیم آن را درک کرده اند.
- از یک فرآیند گام به گام برای یافتن علت اصلی استفاده کنید.از نتیجهگیری عجولانه خودداری کنید.
- علتها را مشخص کنید نه علائم را.
- از منطق استفاده کنید نه احساسات.
- روی اطمینان از دقیق بودن پاسخها تا حد امکان تمرکز کنید.
- هنگام پاسخ دادن به سوالات “چرا” از دیدگاه مشتری استفاده کنید.
- حقایق و دانش باید مبنای هر پاسخ باشد.
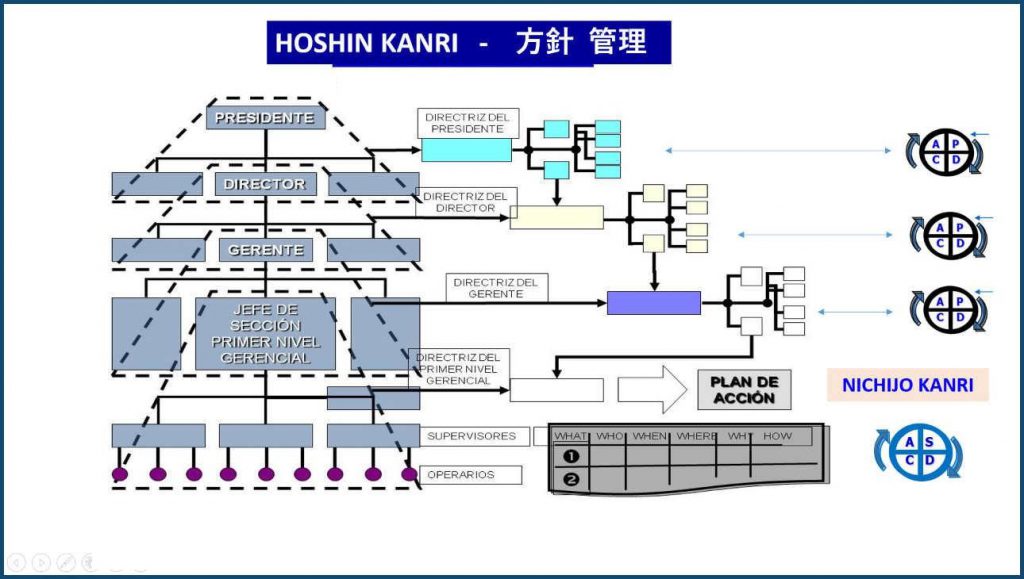