نوشته دکتر محمدرضا عاطفی

مشاور استراتژی و آینده پژوه
عضو هیات علمی دانشگاه
توليد ناب: اصول، عناصر و فلسفه توليد ناب
مقدمه
توليد ناب یک روش تولید است که برای کمک به پاسخگویی سریعتر به مشتریان و تامین کنندگان طراحی شده است. هدف این استراتژی افزایش کارایی با حذف اتلافها، بهینهسازی فرآیندها و کاهش هزینهها است. این کار امکان کاهش ضایعات و هزینههای موجودی را تنها با تولید آنچه مورد نیاز است و نه ذخیرهسازی بیش از حد فراهم میکند. این روش با کاهش زمان تولید، نرخ بهره وری را بهبود میبخشد و به افزایش سود کمک میکند.
تاریخچه توليد ناب
این روش که به عنوان توليد ناب یا تولید به موقع (JIT) نیز شناخته میشود، به اواخر دهه 1940 باز میگردد که تویوتا مدل عملیاتی خود را به نام سیستم تولید تویوتا (TPS) توسعه داد. بعدها، در سال 1988، جان کرافچیک اصطلاح “ناب” را ایجاد کرد.
یک نظریه کمتر مطرح شده آن است که هنری فورد به عنوان اولین فردی بود که یک فرآیند تولید را از ابتدا تا انتها یکپارچه کرد. در حالی که تا دهه 1980 به عنوان توليد ناب نامیده نمیشد، فورد مفاهیم ناب را در خط تولید مدل-T خود با تمرکز بر انتقال یکپارچه قطعات از یک خط به خط دیگر و در عین حال کاهش ضایعات به کار برد. او این کار را با ساختمانهای چند طبقه با کریدورهایی از یک طبقه به طبقه دیگر انجام داد که محصولات را از خطی به خط دیگر منتقل میکرد.
در حالی که نوآوریهای بزرگی از زمان مدل-T انجام شده است، فلسفهها و مفاهیم فورد اساس توليد ناب مدرن است.
قبل از جنگ جهانی دوم، کیچیرو تویودا، رئیس وقت شرکت تویوتا موتور، تفکر و فلسفه فورد را در فرآیندهای تولید تویوتا به کار برد تا کارایی را افزایش دهد. در آن زمان، تویوتا یک شرکت بسیار کوچکتر و منطقهای بود. کیچیرو تویودا اهداف تبدیل شدن به بهترین تولیدکننده را داشت و میدانست که با توليد ناب میتوان به آن اهداف دست یافت. در حالی که نوآوری و بهبود مستمر اجزای کلیدی تویوتا بود، کیچیرو تویودا این فلسفهها را برای توسعه یک شرکت ناب که مظهر بهبود بود، گسترش داد.
تمرکز تویوتا در دهههای 1940 و 1950 بر حذف زمان و مواد تلف شده از هر مرحله از فرآیند تولید – از مواد تا کالاهای نهایی – برای رسیدگی به همان شرایطی طراحی شده بود که اکثر شرکتهای امروزی با آن مواجه هستند: نیاز به فرآیندهای سریع و انعطافپذیر. جفری ک. لیکر در راه تویوتا: 14 اصل مدیریت در مورد: آنچه مشتریان میخواهند، زمانی که آن را میخواهند، با بالاترین کیفیت و هزینه مقرون به صرفه را توضیح میدهد.
در حال حاضر، تویوتا به عنوان نمادی از تولید ناب است که بسیاری از تولیدکنندگان را تشویق میکند که از الگوی خود پیروی کنند. سیستم تولید تویوتا (TPS) نسخه ناب خود تویوتا است. TPS مفاهیم و اصول کلیدی تولید ناب را در بر میگیرد. بسیاری از تولیدکنندگان سعی میکنند مانند تویوتا، تولید ناب را یاد بگیرند و در کارخانههای خود پیادهسازی کنند، اما انجام این کار همیشه آسان نیست.
لیکر توضیح میدهد: «تویوتا همیشه به این فکر میکند که چگونه سیستم ارزشی را آموزش دهد که براساس آن مدیران شرکت را وادار کند تا به کف کارخانه بروند، واقعاً نوآوری کنند و عمیقاً در مورد مسائل بر اساس حقایق واقعی فکر کنند. این پیش فرض نوآوری ناب و حل چالشها است. این روش که از دنیای تولید سرچشمه گرفته است، امروزه با موفقیت به عنوان یک روش مدیریتی در کلیه صنایع تولیدی و خدماتی استفاده میشود.
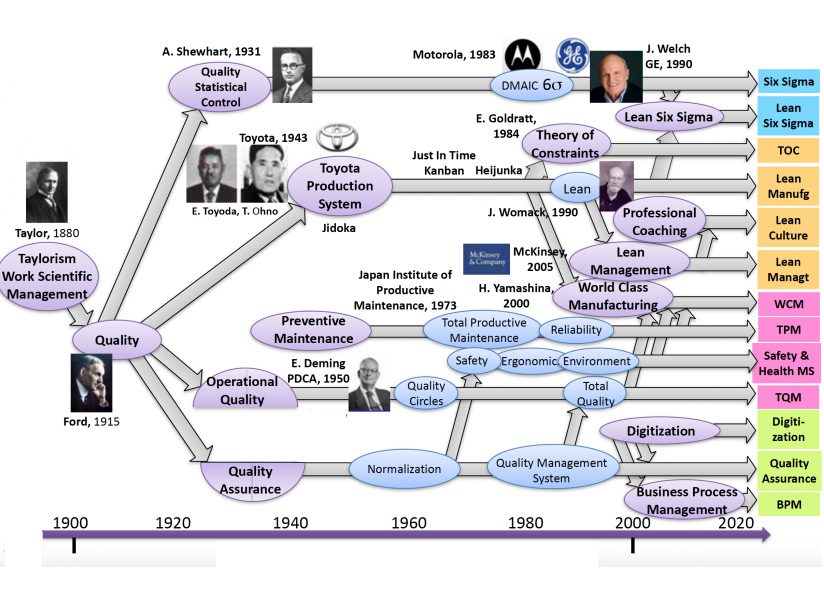
مزایای توليد ناب
قبل از اینکه بخواهید تولید ناب را در تجارت خود پیادهسازی کنید، تجزیه و تحلیل مزایای روش تولید برای همسو کردن انتظارات شما با واقعیت بسیار مهم است. این روش در طول مسیر تکامل خود، پتانسیل خود را برای به ارمغان آوردن موارد زیر ثابت کرده است:
- كاهش موجودي
- افزايش كيفيت
- كاهش نيازمنديهاي فضا
- كوتاهكردن پيشزمان
- افزايش بهرهوري
- انعطافپذيري بيشتر
- ارتباطات متقابل قویتر با تامین کنندگان
- هزينههاي كمتر
- افزايش سود
- افزایش رضایت کارکنان
- افزایش رضایت مشتریان
تعريف كاری توليد ناب
توليد ناب يـك اقـدام گسترده سازماني به منظور ارائه خـروجــي (محـصول) در كوتاهتـرين پيش زمان توليد (Lead Time) ممـكن و پايينترين هزينه كل ممكن بوسيله تشخيص مداوم و از ميان بـرداشتن تمـامي حـالتهاي اتلاف و مغايرت ميباشد. بنابراين JIT در جستجوي :
– حذف اتلافات
– از ميان برداشتن فعاليتهاي فاقد ارزش
مي باشد.
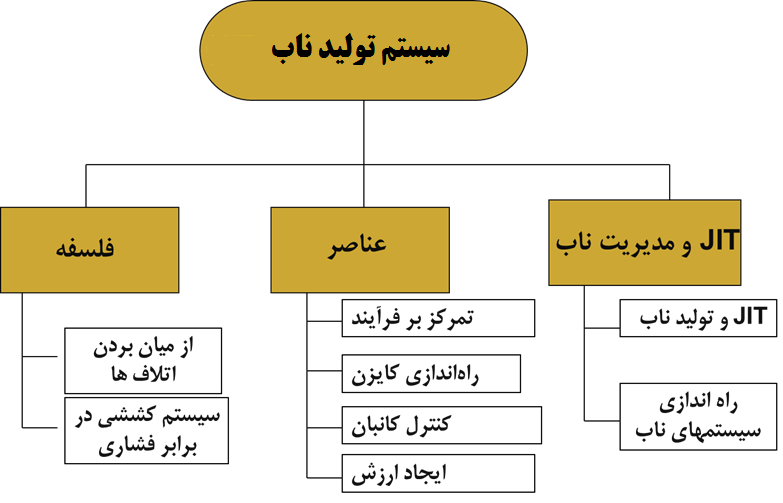
فلسفه توليد ناب
تولید ناب یک تلاش مداوم در حال تحول است که مستلزم درک و مشارکت تمام سطوح یک سازمان است. برای دستیابی به یک عملیات ناب به همان اندازه که اجرای فنی مهم است، تفکر ناب هم مهم است. استراتژیهای مختلفی برای کاهش اتلاف در فرآیند تولید وجود دارد، اما درک و درونی کردن فلسفههای زیربنایی به منظور حفظ یک عملیات ناب و ادامه تلاش برای یک عملیات بی نقص و بدون اتلاف نیز مهم است.
مديريت مبتني بر دانش در سدههاي اول قرن بيستم به طوري عميق پاسخ به يك سوال مهم را مد نظر قرار داد.
اگر در جايي اتلافي هست، چه كسي مسئول آن است؟
مديريت يا نيروي كار؟
دو بنيانگذار مهم مديريت علمي پاسخهاي متفاوتي را ارائه نمودند:
فردريك تيلور(1856 – 1915) معتقد بود هدف اصلي مديريت علمي (مبتني بر دانش) از ميان برداشتن شرايطي بود كه كارگران تعمدا در آن شرايط آهستهتر از حد توانايي كار ميكردند. بنابراين او ميگفت مسئله اتلاف نتيجه اجحاف نيروي كار ميباشد.
فرانك گيلبرت (1868 – 1924) اگرچه معتقد بود مسئله اتلاف نتيجه يك محيط كاري سـخت و بغرنج ميباشد، (ليكن) مسئول آن مديريت است.
اين (موضوع) كه نسخهاي از مديـريت علمي ( مبتني بر دانش) است، توسط فرانك گيلبرت بيان گرديد و تاثير بسزايي بر آغاز JIT داشت. تعداد زيادي از مديـران ژاپني رويكرد گيلبرت را تحت عنوان WWII فرا گرفتند.
تائيچي اونو(1912- 1990) رويكرد JIT (سيستم توليد تويوتا)كه به منظور توليد با كيفيت بالا و ميزان منابع حداقل بود را ايجاد نمود.
۱- از میان بردن اتلافها
اتلاف عبارت است از«استفاده بیشتر از حداقل مقدار مورد نیاز برای ایجاد ارزش افزوده در محصولات از تجهیزات، مواد، اجزا، فضا و وقت کارکنان».
انواع اتلافها
- توليد اضافي (پس فرآوري)
- زمانهاي بي حاصل (تاخيرات يا انتظار )
- حمل و نقل غير ضروري
- فرآيندهاي غير ضروري
- موجودي
- جابجايي زائد
- كيفيت پايين
- عدم استفاده از استعدادها
۲- سیستمهای کششی در مقابل سیستم فشاری
بر خلاف توليد انبوه (سيستم “ فشاري“ )
JIT از ميان سيستمهاي توليد، بمانند واكنشي است نسبت به تقاضاي مشتري
سیستم فشاری
مواد بدون نگرانی درباره اینکه آیا منابع در دسترس هستند یا نه به سوی ایستگاههای کاری هل داده میشوند.
سیستم كششی
مواد درست زمانی که به آن احتیاج باشد به سوی ایستگاه کاری کشیده میشوند.
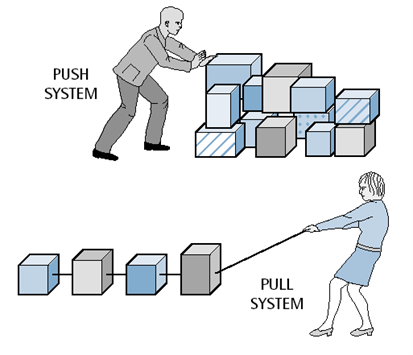
مثال سیستم فشاری
فرض کنید سه ایستگاه کاری داریم.
در ایستگاه کاری یک، تولید هر واحد کالا ۲۰ ثانیه طول میکشد. بنابراین ظرفیت تولید ۱۸۰ قطعه در یک ساعت است و اندازه دسته نیز ۵ میباشد.
در ایستگاه کاری دو، تولید هر واحد کالا ۲۵ ثانیه طول میکشد. بنابراین ظرفیت تولید ۱۴۴ قطعه در یک ساعت است و اندازه دسته نیز ۱۲ میباشد.
تولید هر واحد کالا ۱۵ ثانیه طول میکشد. بنابراین ظرفیت تولید ۲۴۰ قطعه در یک ساعت است از آنجا که ایستگاه سه آخرین ایستگاه است لذا اندازه دسته نداریم.
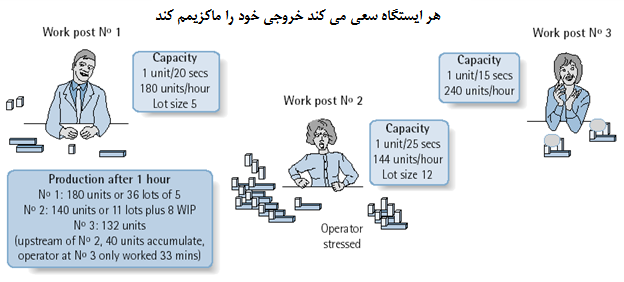
در یک سیستم فشاری تولید در ساعت اول به شرح ذیل خواهد بود:
ایستگاه شماره یک: تعداد ۱۸۰ واحد کالا تولید کرده است. ۳۶ دسته ۵ تایی
ایستگاه شماره دو: تعداد ۱۴۰ واحد کالا تولید کرده است. ۱۱ دسته ۱۲ تایی بعلاوه ۸ کالای در حین ساخت. لازم به ذکر است که ایستگاه دو باید منتظر اولین دسته ۵ تایی از ایستگاه اول باشد که در این صورت ۱۰۰ ثانیه اول تولید را از دست داده و منتظر رسیدن آن میباشد. لذا ۴ واحد کمتر از ظرفیت تولید میکند.
ایستگاه شماره سه: تعداد ۱۳۲ واحد تولید کرده است. لازم به ذکر است که ایستگاه سه باید منتظر اولین دسته ۱۲ تایی باشد که از ایستگاه دوم به آن میرسد. این ایستگاه تنها ۱۱ دسته ۱۲ تایی یعنی ۱۳۲ تا را در طی یک ساعت دریافت خواهد کرد. در نهایت تولید نهایی ۱۳۲ تا خواهد بود.
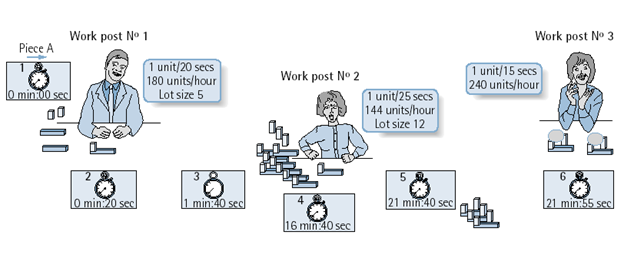
مثال سیستم کششی
مهمترین ویژگی تولید کششی یکسانسازی تولید با تقاضا است. در این روش، اندازه دسته = ۱
فرض کنید سه ایستگاه کاری داریم.
در ایستگاه کاری یک، تولید هر واحد کالا ۲۰ ثانیه طول میکشد. بنابراین ظرفیت تولید ۱۸۰ قطعه در یک ساعت است و اندازه دسته نیز ۱ میباشد.
در ایستگاه کاری دو، تولید هر واحد کالا ۲۵ ثانیه طول میکشد. بنابراین ظرفیت تولید ۱۴۴ قطعه در یک ساعت است و اندازه دسته نیز ۱ میباشد.
در ایستگاه کاری سه، تولید هر واحد کالا ۱۵ ثانیه طول میکشد. بنابراین ظرفیت تولید ۲۴۰ قطعه در یک ساعت است از آنجا که ایستگاه سه آخرین ایستگاه است لذا اندازه دسته نداریم.
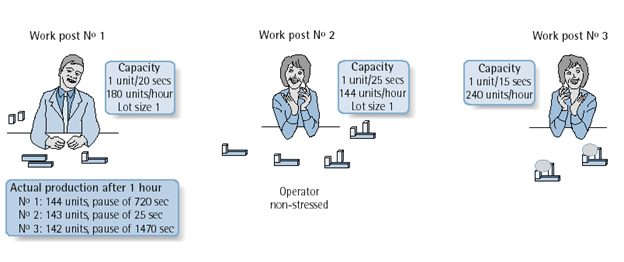
با این تغییر در ایستگاه یک ما ۱۴۴ واحد محصول تولید خواهیم کرد. در ایستگاه دو ۱۴۳ واحد و در ایستگاه ۳ هم ۱۴۲ واحد کالا تولید خواهیم کرد.
در مرحله بعد برای اینکه تولید را از همین خط تولید بدون افزایش ظرفیت تولید ایستگاه دو و سه را با هم ترکیب میکنیم و بنابراین به طور متوسط هر کالا ۲۰ ثانیه تغییر میکند. در این صورت میزان تولید در هر ایستگاه ۱۸۸ خواهد بود.
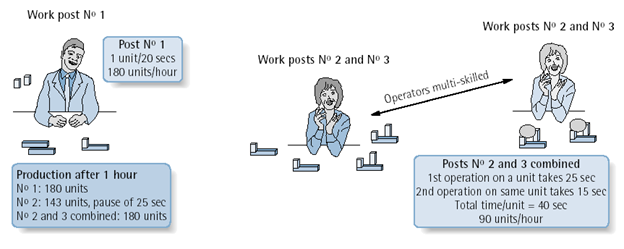
در روش فشاری ما به دنبال تمرکز بر بکارگیری بیشتر از هر ایستگاه کاری خواهیم بود. بهره وری و راندمان تولید هر ایستگاه تولیدی مهمترین هدف در سیستم فشاری است. در این صورت در ایستگاههای غیر گلوگاهی بیشتر از حد نیاز تولید خواهد شد. موجودی حین تولید در تمام ایستگاهها افزایش خواهد یافت. و موجودی بالا سبب خواهد شد بسیاری از مشکلات در حین تولید پنهان بماند.
در روش کششی تولید در هر ایستگاه تنها به میزانی که نیاز است صورت خواهد گرفت. در این صورت نیاز است در تمام ایستگاههای غیرگلوگاهی ظرفیت تولید کمتر باشد. عدم تولید اضافی در ایستگاهها سبب خواهد شد تا بسیاری از مشکلاتی که سبب اختلال در فرآیند تولید میشد هویدا شود. این کار سبب خواهد شد تا شرکت فرصتهای رشد تولید را بدست آورد.
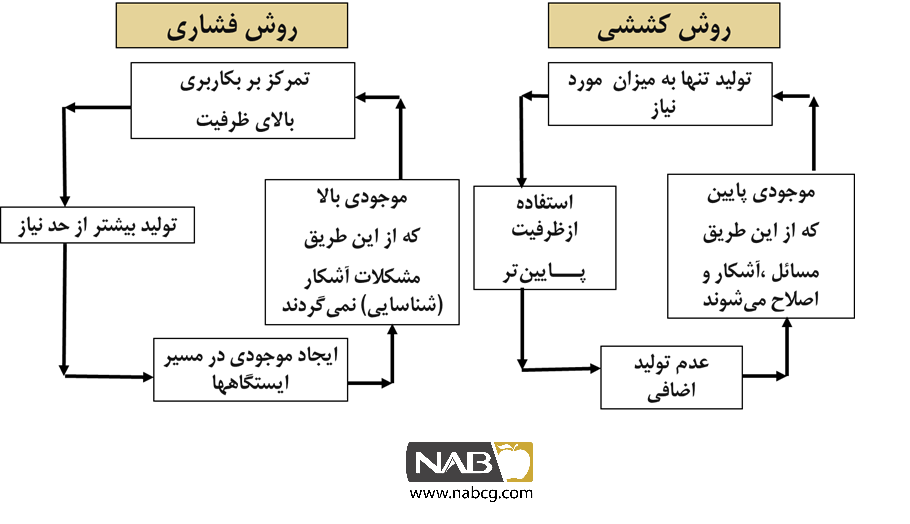
رويكرد اونو
اونو انديشههاي مهمي را براي تولید ناب و JIT از دو اصل اساسي امريكايي اقتباس نمود:
- توليد انبوه فورد و
- سوپرماركت
توليد استاندارد شده فورد به اونو ارزش سازگاري و كاهش تغييرپذيري در توليد را آموخت.
سوپرماركت امريكايي به اونو نشان داد كه از مشتري ميتوان [اينكه]
- چه نياز دارد؟
- چه زمان نياز دارد؟
- چه ميزان نياز دارد؟
را اخذ نمايد.
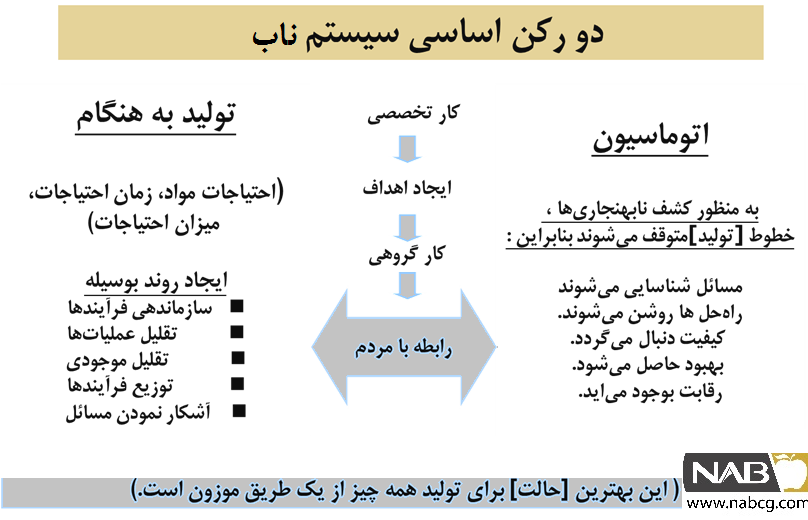
عناصر توليد ناب
۱- تمرکز فرآیندی
تفكر فرآيندي باعث ايجاد JIT نمي شود، اما از بيشترين كاربردهاي كامل آن محسوب ميشود.
يك فرآيند، مجموعه از عناصر است كه با يكديگر درتعامل بوده و تعيين كننده عملكرد خروجي ميباشند.
مباني تفكر فرآيندي عبارتند از:
- شركت توسط فرآيندها معماري ميشود.
- فرایندها میتوانند ارزشی که یک شرکت خلق میکند را شناسایی کند.
- به منظور بهبود، ما بايد فرآيندهاي بحراني را شناسايي و تغيير دهيم.
- ظرفيت و فرآيندها با هم لينك ميشوند.
فرآيندها ميتوانند توسط 5 عنصر(فاكتور) عمده كه آن را تشكيل ميدهند، توصيف شوند.
- فعاليتها
- وروديها / خروجيها / جريانها
- ساختار
- منابع
- استاندارد
روش تفكر فرآيندي در [قالب] چهار قاعده سيستم توليد تويوتا TPS مـطرح ميگردد:
- قاعده 1 : جزئيات، توالي، زمان و خـروجي تمامي كارها ميبايست مشخص شود.
- قاعده 2: هرگونه ارتباط با مشتري و تامين كننده ميبايست مديريت گردد.
- قاعده 3 : مسير كلي هر محصول يا خدمت ميبايست ساده و قابل اداره كردن شود.
- قاعده 4 : هر بهبود ميبايست مطابق با روشهاي عـلمي، با رهبري يك (مربی) و از پايينترين سطح سازمان ايجاد گردد.
۲- کایزن
كايزن (بهبود مستمر): (براساس منطق كايزن) بهبود هرگز پايان نميپذيرد. و لذا مايل به شفاف سازي توسط موارد زير است :
- رویکرد از بالا به پایین
- عملگرایی
- شاخصهاي اندازهگيري صريح و قابل بازبيني
- تكرار اين روند همانند چرخه (PDCA)
اثر مرکب: اصل به دست آوردن نتایج بزرگ از طریق مجموعهای از انتخابهای کوچک و مستمر است.
اگر روزی 5 صفحه کتاب بخوانیم (25 روز در ماه):
- در ماه 125 صفحه
- در سال 1500 صفحه
- در پنج سال 7500 صفحه
اگر روزی 30 دقیقه کمتر در شبکههای اجتماعی وقت بگذرانیم:
- در ماه 15 ساعت وقت آزاد میشود.
- در سال 180 ساعت وقت آزاد میشود.
- در پنج سال 900 ساعت وقت آزاد میشود.
۳- کانبان
سيستم كانبان به چندين هدف براي تويوتا بكار ميرود :
- راهنمايي است براي فرآيندهاي متقدم به منظور ارسال (خروجي) بيشتر
- ابزار كنترل بصري است به منظور نشان دادن نواحي با توليد بالا(بيش از حد) و عدم انطباق.
- خود ابزاري است براي كايزن.
۴- ارزش آفرینی
در تولید ناب مهمترین هدف، خلق ارزش برای مشتریان است. در این سیستم تولید ارزش از منظر مشتری تعریف میشود. برای ارزش میتوان از فرمول زیر استفاده کرد:
ارزش = کارایی / هزینه
اصول تولید ناب و چرخه اجرای ناب
- شناسايي ارزش از وجه مشتري
- شناسايي جريان ارزش صحيح و رفع اتلاف
- حفظ جریان ارزش آفرین از منظر مشتری
- طراحي و آماده سازي چيزي كه مشتري ميخواهد (خواسته مشتري) دقيقا در زماني كه آنرا ميخواهد.
- پيگيري كمال، تجزيه و تحليل پي در پي و بهبود جريان فرآيند.