نوشته دکتر محمدرضا عاطفی

مشاور استراتژی و آینده پژوه
عضو هیات علمی دانشگاه
ابزارها و تکنیکهای تولید ناب
بخش سوم
۱۸- تولید سلولی
تولید سلولی چیست؟
در زیست شناسی، سلول کوچکترین واحد حیات است که می تواند به تنهایی زنده بماند.
استفاده از این ایده در تولید، ساخت سلولی و مفهوم ایجاد واحدهایی به نام سلول های تولیدی را به ما می دهد. این سلولهای تولیدی را میتوان نسخههای مینیاتوری طرحبندی گیاهی در نظر گرفت که قادر به تولید یک محصول کامل یا یک خانواده محصول است.
سلولهای تولیدی به گونهای طراحی میشوند که هر سلول از تمام ماشین آلات و نیروی کار مورد نیاز برای تولید یک محصول یا یک خانواده محصول مشابه یکدیگر تشکیل شده است. از آنجایی که ماشینهای چند منظور مختلفی در یک سیستم تولید سلولی وجود دارد، لذا بر آموزش نیروی کار چندمهارت تمرکز میکنند تا بتوانند به راحتی با تمام ماشینآلات درون یک سلول کار کنند. این کار تکنسینها را تشویق میکند تا خلاق باشند و بهبودهای فرآیندی را پیشنهاد کنند تا نقصهای کمتری تولید شود و بازده تولید محصول نیز افزایش یابد.
در یک محیط کاری، کارگران بخشهای مختلف در نزدیکی یکدیگر در یک سلول قرار میگیرند تا جریان کار را افزایش دهند، زمان پاسخگویی به مشتری را کاهش دهند، اتلافها را حذف میکنند و موانع و سیلوهای بین بخشها را از بین ببرند. در تولید سلولی غالبا نوع سازماندهی ماشین آلات براساس محصول یا خانواده محصول صورت میگیرد به همین دلیل پیشنیاز آن تکنولوژی گروهی است.
ویژگیهای ساخت سلولی
- ماشینهای درون یک سلول نزدیک به هم گروهبندی میشوند، به طوری که میتوان قطعات ناتمام را از یک ماشین به ماشین دیگر برد.
- کارکنان ممکن است بیش از یک ماشین را در سلول تولید کار کنند.
- قطعات پردازش شده از طریق سلول ویژگیهای مشابهی دارند، به طوری که تنظیمات دستگاه به حداقل می رسد.
- احتمالاً تعدادی سلول تولیدی در فرآیند تولید وجود دارد.
مزایای ساخت سلولی
- گروهبندی محصولات مشابه به منظور کاهش زمان تغییر
- استفاده موثر از فضا در طول کل فرآیند تولید
- افزایش انعطاف پذیری و شفافیت
- کاهش زمان تحویل
- افزایش بهرهوری کل
- افزایش کار گروهی و ارتباط بین کارکنان و بخشها
نمونهای از ساخت سلولی
یک جعبه فلزی به کارخانه میرسد و باید مونتاژ شود. مونتاژ به مراحل مختلفی نیاز دارد. هدف از ساخت سلولی این است که تمام مراحل در یک منطقه و در یک سلول واحد اتفاق بیفتد. این امر زمان حمل و نقل قطعات را در طول فرآیند تولید کاهش میدهد.
مرسدس بنز اخیراً تولید سدان سایز متوسط خود، کلاس C را در کارخانه خود در برمن در کنار شاسی بلندهای GLC و GLC کوپه و شاسی بلند EQC تمام الکتریکی آغاز کرده است. این کارخانه طیف کاملی از پیکرهبندیهای خودروهای خود را با طیف متنوعی از پیشرانه و بدنه مونتاژ شده در یک خط طراحی کرده است. اکنون کارخانه باید با تنوع بسیار بیشتری نسبت به زمانی که تولید خودروی سواری را در سال 1974 تنها با یک مدل به نام استات اس ۱۲۳ در این سایت تولیدی آغاز کرد، کنار بیاید.
بنابراین، انعطاف پذیری امری ضروری است، و برای این کار مرسدس یک سیستم جدیدی طراحی کرده است که در آن سلولهای تولیدی برای کارگاه بدنه طراحی شده است و با افزایش انعطافپذیری امکان تولید محصولات متنوع در یک خط تولید فراهم میشود.
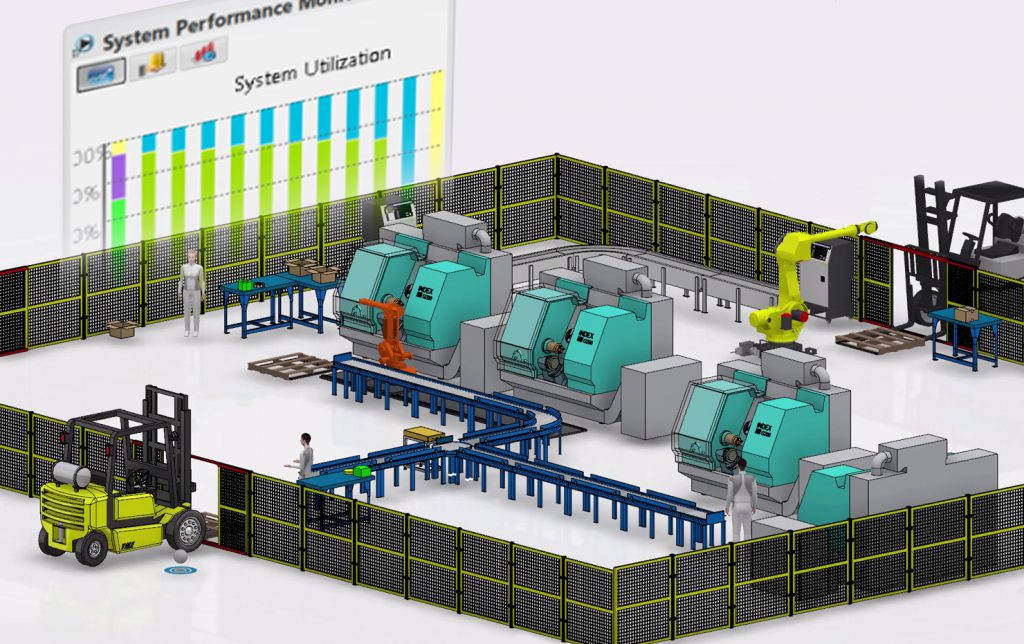
۱۹- تغییر سریع Quick Changeover
تغییر سریع و کاهش زمان راهاندازی
در اقتصاد امروز، زمان پول است. مدت زمان صرف شده برای تعویض ماشین میتواند پرهزینه باشد. به همین دلیل است که تعداد فزایندهای از تولیدکنندگان از روشهای کاهش زمان راهاندازی و تغییر سریع استفاده میکنند. تکنیکهای صرفه جویی در پول ابزاری برای تولید ناب است که بر حذف اتلافها در عملیات تولید تمرکز دارد.
اکنون تنوع محصولات تولیدی به شدت در حال افزایش است و اندازه دستههای تولیدی نیز مرتبا در حال کوچک شدن هستند. برای این منظور لازم است تا زمان راهاندازی کاهش یابد تا امکان بهبود جریان نقدی و سودآوری فراهم گردد. این کار برای بقای تولیدکنندگان بسیار مهم است. بسیاری از شرکتها بیش از 20 درصد از زمان تولید برنامهریزی شده خود را صرف تغییر خطوی تولید از یک محصول به محصول دیگر میکنند. مفهوم اصلی تغییر سریع، کاهش زمان راهاندازی است که مستقیماً منجر به اندازههای دستهای کوچکتر برای قطعات میشود و به سازنده اجازه میدهد فقط آنچه را که مشتری درخواست میکند تولید کند.
نمونهای از تغییر سریع؟
خدمه پیت در یک مسابقه اتومبیل رانی یک نمونه عالی از تغییر سریع است. هرچه یک خدمه سریعتر بتواند تغییر کند، شانس بیشتری برای برنده شدن یک مسابقه دهنده خواهد داشت. یک تغییر آهسته اغلب منجر به از دست دادن یک مسابقه میشود.
مزایای تغییر سریع
مزایای اصلی تغییر سریع خط تولید و کاهش زمان راهاندازی عبارتند از:
- نیاز به فضای کمتر
- هزینه کمتر بابت موجودی
- کار کمتر برای مدیریت موجودی
- افزایش ظرفیت تولید با کاهش زمان راهاندازی ماشین آلات
- استانداردسازی بیشتر ابزارها و روشهای راهاندازی
- از رده خارج شدن کمتر به دلیل منسوخ شدن
مهمترین ابزار تغییر سریع استفاده از تعویض یک دقیقهای قالب SMED است.
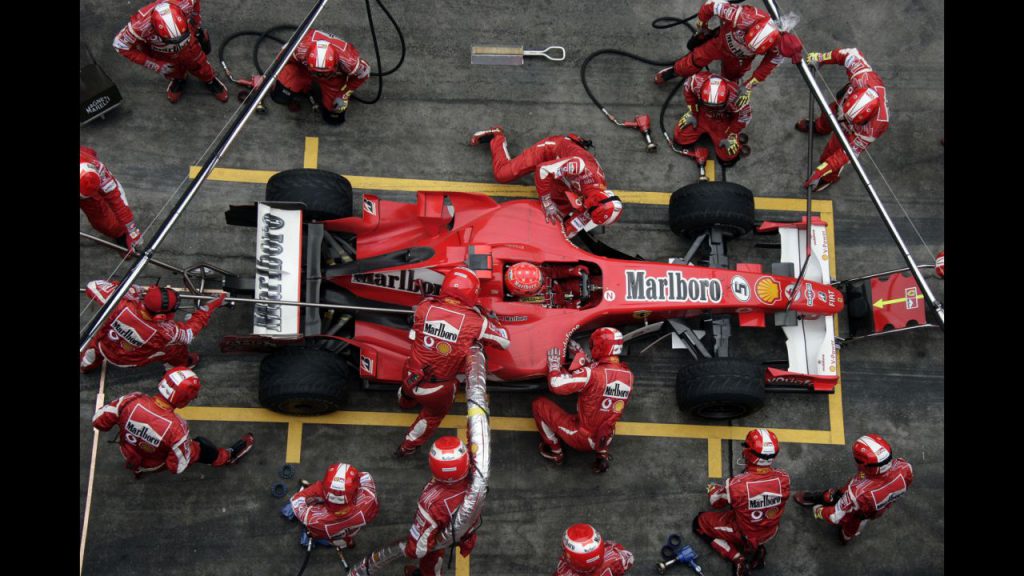
۲۰- تعویض یک دقیقهای قالب Single-minute Exchange of Die (SMED)
تعویض یک دقیقهای قالب چیست؟
SMED سیستمی برای کاهش چشمگیر زمان لازم برای تعویض تجهیزات یا تغییر خط تولید از یک محصول به محصول دیگر است. ماهیت سیستم SMED این است که تا آنجا که ممکن است مراحل تغییر را به “خارجی” (که در حین کار تجهیزات انجام می شود) تبدیل کند و مراحل باقی مانده را ساده و ساده کند. نام تبادل یک دقیقهای قالب از هدف کاهش زمان تغییر به “تک رقم” (یعنی کمتر از 10 دقیقه) میآید.
با کاهش زمان راه اندازی، کارخانهها میتوانند کارایی را تا حد زیادی بهبود بخشند. SMED توسط فردریک تیلور در سال 1911 ابداع شد و بعداً توسط فورد موتورز در سال 1915 مورد استفاده قرار گرفت.
نمونههایی از SMED
یکی از نمونههای واقعی SMED را میتوان در طول مسابقات اتومبیلرانی حرفهای مشاهده کرد. سرعت تیم پشتیبانی راننده (خدمه پیت) اغلب میتواند تفاوت بین برد و باخت را برای رانندگان اتومبیلهای مسابقهای ایجاد کند. خدمه پیت معمولاً از هر فرآیند تعویض لاستیک، سرویس و سوخت رسانی فیلم میگیرند و دائماً به دنبال راههایی برای سرعت بخشیدن به زمان ماندن ماشین در بخش سرویس خودروی مسابقهای هستند. زمان صرف شده برای هر عملیات تجزیه و تحلیل میشود – تعویض لاستیک، تمیز کردن شیشه جلو و سوخت رسانی.
اتفاق دیگری هر روز در صنعت رستوران رخ میدهد. بسیاری از رستورانها سه منوی صبحانه، ناهار و شام را ارائه میدهند. تغییر از یک منو به منوی دیگر میتواند تا یک ساعت طول بکشد تا زمانی که آشپزخانهها برای وعدههای غذایی مختلف آماده میشوند. تسریع این فرآیند باعث میشود تا انتقال راحتتری بین زمانهای سرو انجام شود. در برخی موارد، رستورانها آنقدر در آن خوب شدهاند که در هر زمانی از روز آیتمهایی را از دو منو – گاهی هر سه – ارائه میکنند.
مراحل اجرا
۱) شناسایی عملیات تعویض قالب: تمامی عملیات انجام شده باید شناسایی و زمان آن اندازهگیری شوند، از جمله زمان انتظار
۲) جدا کردن عملیات داخلی و خارجی: عملیات تغییر خط تولید و راه اندازی را به دو گروه عملیات داخلی و خارجی تقسیم کنید.
- عملیات داخلی شامل آن دسته از فعالیتهای تعویض ابزار میشوند که نیاز به توقف تولید دارند
- عملیات خارجی آنهایی هستند که میتوانند قبل یا در حین تولید انجام شوند: آماده سازی قطعات یا ابزارها، تنظیمات از پیش...
۳) گروهبندی عملیات خارجی با هم: این گروهبندی با حذف زمان فعالیتهای خارجی از زمان توقف، زمان توقف تولید را کاهش میدهد.
۴) زمان انجام عملیات داخلی را کاهش دهید: هر یک از این عملیات را با جزئیات مرور کنید و تعیین کنید که آیا میتوان آنها را حذف، اصلاح، یا تسریع کرد مانند استفاده از جیگ و فیکسچر.
۵) کاهش زمان عملیات خارجی: تاثیر مستقیمی ندارد اما با این وجود میتواند کارایی را از طریق مثلا اجرای عملیات به صورت موازی یا استانداردسازی بهبود بخشد یا هزینهها را کاهش دهد.
البته تکمیل این روش با استانداردسازی یا مراحل بهبود مستمر امکان پذیر خواهد بود.
تکنیکهای مورد استفاده
- تا حد ممکن تبدیل فعالیتهای داخلی راهاندازی به خارجی
- استاندارد کردن فعالیتها
- سادهسازی راه اندازی داخلی
- بیشتر کردن عملیات موازی
- حذف بعضی از تنظیمات
- افزایش مکانیزاسیون
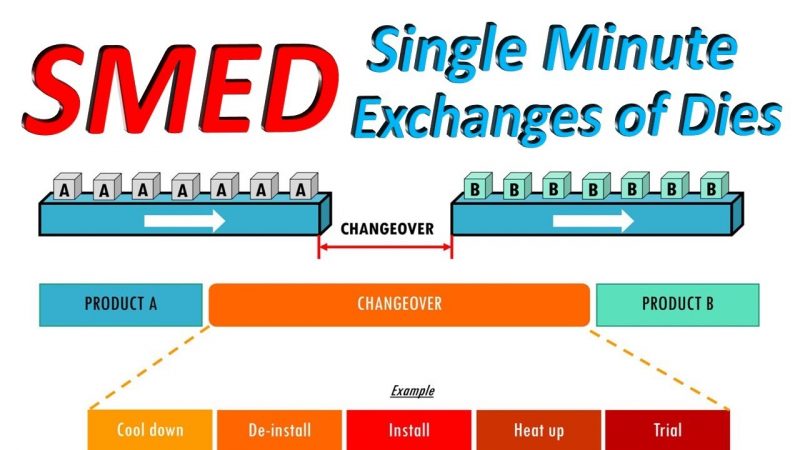
۲۱- شش ضرر بزرگ Six big losses
شش ضرر بزرگ چیست؟
تعمیر و نگهداری تجهیزات یک اولویت در هر مرکز تولیدی است. اپراتورهای ماشین آلات، تکنسینها و سایر کارکنان باید اطمینان حاصل کنند که همه چیز برای تولید به موقع محصولات به طور موثر انجام میشود. با این حال، ممکن است همیشه به دلیل رویدادهای غیرمنتظره مانند خرابی تجهیزات امکان پذیر نباشد. اینجاست که درک شش ضرر بزرگ مفید است.
شش ضرر بزرگ به عنوان راهی برای طبقه بندی انواع مسائل مرتبط با کند شدن تولید تعریف شده است و به شرکتها کمک میکند تا مناطقی را برای بهبود فرآیندهای تولید و بهرهوری در کف کارخانه شناسایی کنند.
شش ضرر بزرگ در دستهبندی اتلافهای مبتنی بر تجهیزات مفید هستند. ضررها عبارتند از توقفهای برنامهریزی نشده، توقفهای برنامهریزی شده، توقفهای کوچک، چرخههای آهسته، مردودیهای تولید و مردودیهای راه اندازی.
شش زیان بزرگ شش دسته از کاهش بهرهوری هستند که تقریباً در سطح جهانی در تولید تجربه میشوند.
عناصر شش ضرر
- خرابیها – توقفهای برنامهریزی نشده زمانی اتفاق میافتد که تجهیزاتی که برای تولید برنامهریزی شدهاند به دلیل یک رویداد برنامهریزی نشده کار نمیکنند.
- راه اندازی/تنظیمات – توقفهای برنامهریزی شده دورههایی از زمان هستند که در آن تجهیزات برای تولید، برنامهریزی شده است اما به دلیل یک رویداد برنامهریزی شده مانند تعویض و تنظیمات ابزار، تمیز کردن یا بازرسیها، کار نمیکند.
- توقفهای کوچک زمانی اتفاق میافتند که تجهیزات برای مدت کوتاهی(معمولا یک یا دو دقیقه) قبل از اینکه اپراتور آن را برطرف کند، متوقف میشود.
- کاهش سرعت – چرخههای آهسته زمانی رخ میدهند که تجهیزات کندتر از زمان چرخه ایدهآل (سریعترین زمان ممکن برای تولید یک قطعه از نظر تئوری) کار میکنند.
- مردودیهای تولید – به قطعات معیوب ایجاد شده در طول تولید با ثبات یا پایدار اشاره دارد.
- مردودیهای راه اندازی یا شروع تولید – قطعات معیوبی هستند که در از زمان راهاندازی تا رسیدن به تولید پایدار، تولید میشوند.
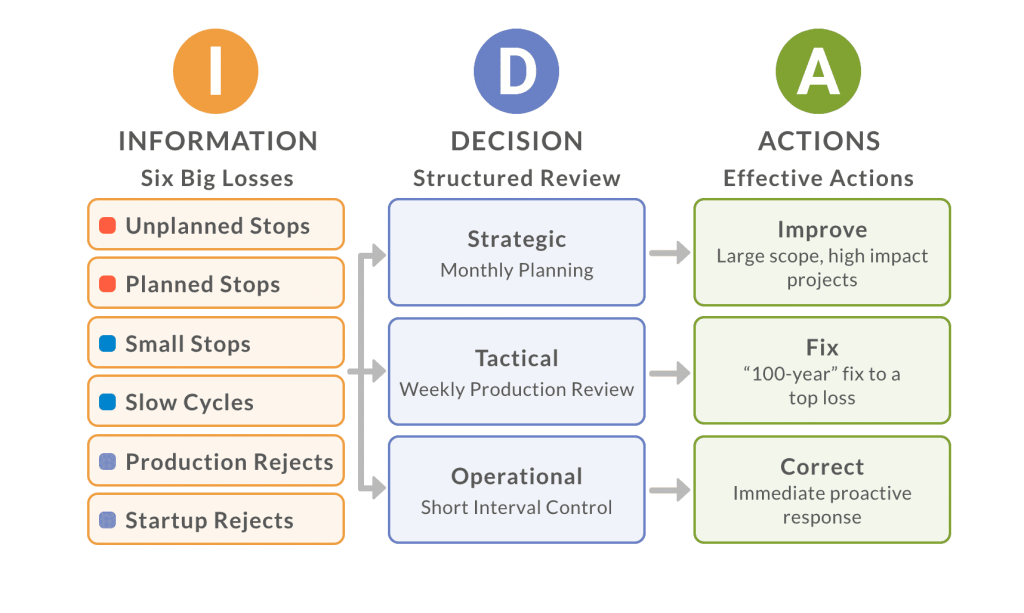
۲۲- مدیریت بصری Visual Management
مدیریت بصری چیست؟
مدیریت بصری یک ابزار کاملا ضروری در دنیای ناب است و میتواند به عنوان رابط بین دادهها و افراد دیده شود. مدیریت بصری از نشانههای بصری غریزی استفاده میکند تا اطلاعات مختصر و دقیق را در یک محل کار همیشه در دسترس کسانی قرار دهد که نیاز به دانستن آن دارند. این اطلاعات به ابتدایی ترین شکل خود فشرده شده است تا همه چیزهایی را که نیاز دارید بدانید.
مدیریت بصری و کنترلهای بصری دست به دست هم میدهند، آنها رگ حیات یک سیستم تولید ناب هستند. مدیریت بصری برای ایجاد یک محل کار بصری با کنترلهایی طراحی شده است که بدون کلمات و وقفه در فرآیند ارتباط برقرار میکنند. کنترلهای بصری این پتانسیل را دارند که به شناسایی مشکلات، کاهش ضایعات، کاهش هزینههای تولید، کاهش زمان تحویل، کاهش موجودی، ایجاد یک محیط کاری امن و حتی افزایش سود شما کمک کنند.
مدیریت بصری توانایی یک سیستم برای نشان دادن سریع وضعیت فعلی به تمام اشخاص درگیر در عرض ۳۰ ثانیه است. این ممکن است وضعیت تولید، استانداردهای کیفیت، وضعیت تحویل یا وضعیت ماشین باشد. شاخصهایی وجود دارد که به همه اجازه میدهد از نحوه ردیابی همه چیز مطلع شوند. اگر مدیریت بصری به خوبی انجام شده باشد، اگر مسئلهای وجود داشته باشد، همه در کارخانه شما از آن مطلع میشوند و درعین حال میدانند که چگونه باید مسئله را حل کنند.
این عامل اصلی در دستیابی به مشارکت کارکنان است و قدرت ایجاد مالکیت اهداف و اشتیاق برای بهبود را نزد کارکنان دارد. این ابزار دارای قدرت خلق یک جو دوستانه و مسئولانه است، و روشی برای بسترسازی فرهنگ بهبود مستمر است.
مدیریت بصری همچنین شفافیت را نشان میدهد و فاصله بین مدیریت و سایر سطوح کارکنان را از بین میبرد. اطلاعات پنهان نیست و کل شرکت بر روی اهداف یکسانی متحد شده و حول نتایج عملکردی متمرکز شده است.
مدیریت بصری چگونه کمک میکند؟
مدیریت بصری وضعیت و شرایط فرآیندهای تولید را به راحتی در دسترس و بسیار واضح برای همه قرار میدهد.
اهداف مدیریت بصری
- شفاف کردن اتلافها و نتایج کلیدی عملکرد
- نمایش مسائل به روشی ساده تر
- شفاف شدن اهداف کارایی
- افزایش ارتباطات موثر
مدیریت بصری در کجا بهترین کاربرد را دارد؟
مدیریت بصری، در جایی که احتمال بروز خطا وجود دارد، چندین کارگر یک کار را انجام میدهند، یا برای تصمیم گیری نیازمند دسترسی سریع به اطلاعات هستیم، کاربرد را دارد. دستورالعملهای کار اغلب میتوانند سادهتر شوند و درک آنها با گنجاندن وسایل کمک بصری بسیار آسانتر باشد. به عنوان مثال، اگر یک واحد باید یک قطعه مبلمان را از چندین قسمت بسازد، اغلب در قالب بصری بهتر درک میشود. مخصوصاً برای کارهایی که توضیح آنها تنها با کلمات دشوار است. مثال دیگر ممکن است نشان دادن عکسی از یک عیب ظاهری برای آموزش و کنترل یکسان بین تمام اپراتورها باشد.
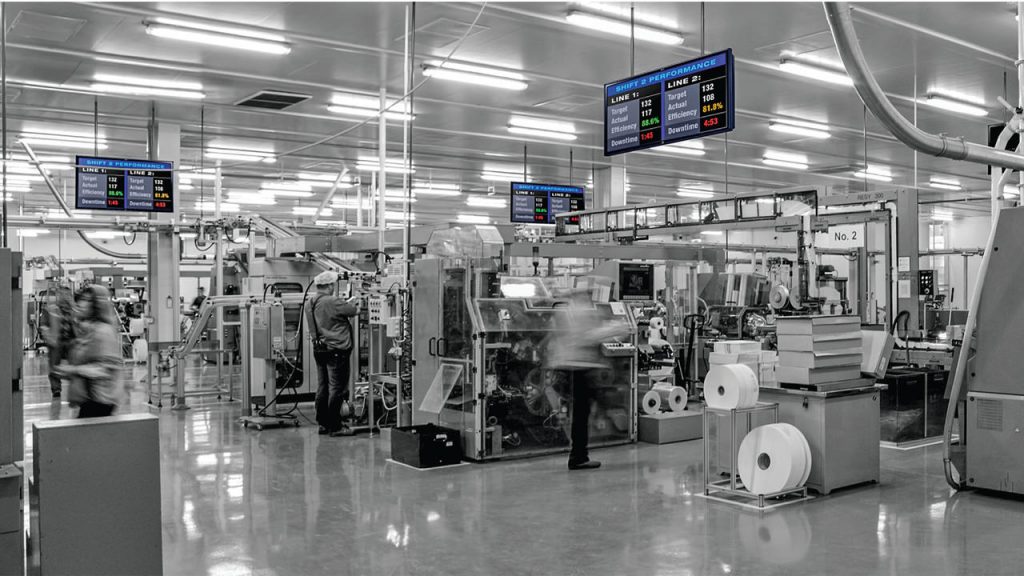
۲۳- مدیریت تقاضا Demand Management
مدیریت تقاضا چیست؟
مدیریت تقاضا یک ابزار ناب است که برای شناسایی تمام تقاضاهای ناشی از یک محیط خارجی، مدیریت آن و وارد کردن آن به زنجیره تامین در یک شرکت استفاده میشود.
این فرآیند به روشی یکپارچه برای کنترل و ردیابی نیازمندیهای واحد کسب و کار و عملیات خرید داخلی تبدیل میشود. این بر حجم محصولات خریداری شده از تامین کنندگان تمرکز میکند به جای توجه بیش از اندازه بر قیمت گذاری تک محصولی، که در فرآیندهای منبع یابی سنتی رایج بود. از طریق فرآیند مدیریت تقاضا، سازمانها عوامل مخارج خارجی را بررسی میکنند، سفارشات خرید را به درستی ترتیب میدهند و اتلافها را در تمام جنبههای فرآیند حذف میکنند.
در مدیریت تقاضا، کنترل تقاضا یک اصل بسیار مهم است. بر همسویی عرضه و تقاضا تمرکز میکند، به ویژه در جاهایی که تغییر ناگهانی و غیرمنتظره در تقاضا وجود دارد. این تغییرات زمانی اتفاق میافتد که تقاضای کوتاهمدت از عرضه پیشی بگیرد یا زمانی که سفارشهای واقعی کمتر از برنامهریزی شده باشد. این میتواند منجر به تصمیمات بسیار واکنشی شود که تأثیر منفی بر حجم کار، هزینهها و رضایت مشتری دارد. تعریف سنجههای عملکردب برای پیگیری تقاضا و مداخله بالقوه حیاتی است. دادههای عملکرد جمعآوریشده میتواند منجر به پیشبینی تقاضای بهتری شود، که ممکن است با یک برنامه گسترده ارتباطات با تأمینکننده یکپارچه شود. این جزئیات به تأمینکنندگان و سازمانها کمک میکند تا داراییها را به طور مؤثرتری مدیریت کنند، و هزینهها را کاهش دهند.
هدف مدیریت تقاضا
مدیریت تقاضا سه هدف اصلی دارد:
- بهبود دقت پیش بینی
- کاهش سرمایه گذاری در موجودی
- تعادل موثرتر بین عرضه و تقاضا
مدیریت تقاضا چگونه اجرا میشود؟
عنصر اصلی اجرای مدیریت تقاضا، ایجاد یک زنجیره تامین شفاف تر است. شرکتها باید از شفافیت همه تامینکنندگانی که با یک شرکت کار میکنند، از بزرگترین تا کوچکترین، اطمینان حاصل کنند. با اطمینان از شفاف بودن هر بازیکن در زنجیره تامین، میتوانید شروع به ایجاد یک زنجیره تامین کارآمدتر کنید.
در مرحله بعد، شرکتها باید تعیین کنند که کدام موجودی غیرضروری است و میتواند کاهش یابد. داشتن موجودی بیش از حد گران است و نگهداری آن دشوار است. در نهایت، این تکنیک محصولات را به طور موثرتری به دست مصرف کنندگان میرساند.
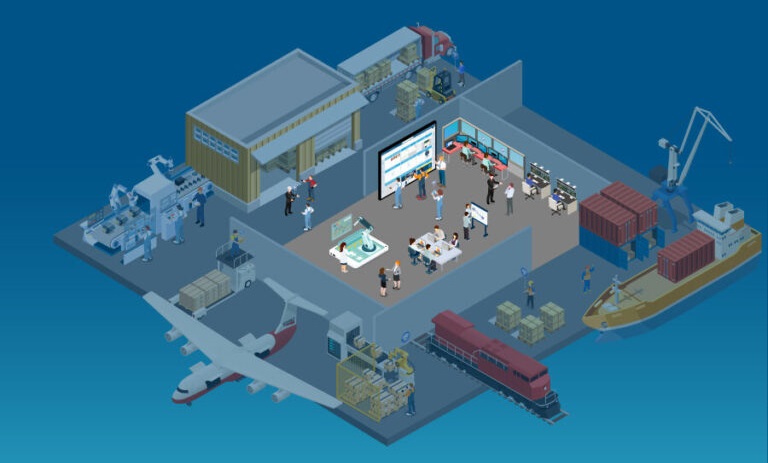
۲۴ – 5S چیست؟
روش 5S به پنج اصطلاح ژاپنی و انگلیسی اشاره دارد که با S شروع میشوند و یک روش سازماندهی محل کار را ارائه میدهند. 5S سیستمی برای کاهش ضایعات و بهینه سازی بهره وری از طریق حفظ یک محل کار منظم و استفاده از نشانههای بصری برای دستیابی به نتایج عملیاتی قوی تر است. اجرای این روش، محل کار را اساساً در پیکربندی موجود آن «پاکسازی» و سازماندهی میکند و معمولاً اولین روش ناب است که سازمانها اجرا میکنند.
عناصر 5S
- مرتب سازی (Seiri): مواد را مرتب کنید و فقط موارد ضروری را که برای تکمیل کارها لازم است نگه دارید. (این عمل شامل مرور تمام محتویات یک فضای کاری است تا مشخص شود کدام یک مورد نیاز است و کدام یک را میتوان حذف کرد. هر چیزی که برای تکمیل یک فرآیند کاری استفاده نمی شود باید منطقه کار را ترک کند.)
- سازماندهی (Seiton): اطمینان حاصل کنید که همه اقلام سازماندهی شده اند و هر مورد یک مکان مشخص دارد. تمام موارد باقیمانده در محل کار را به روشی منطقی سازماندهی کنید تا انجام وظایف برای کارگران آسانتر شود. این اغلب شامل قرار دادن اقلام در مکانهای ارگونومیک است که افراد برای رسیدن به آنها نیازی به خم شدن یا انجام حرکات اضافی ندارند.
- تمیز کردن/ نظافت Shine (Seiso): محل کار را تمیز و بازرسی کنید. با خلاص شدن از شر کثیفیها، زبالهها و غیره میتوانید به راحتی مسائل موجود در فرآیند تولید را شناسایی کنید. تلاشهای پیشگیرانه برای تمیز و منظم نگه داشتن محل کار برای اطمینان از کار هدفمند است. این به معنای تمیز کردن و حفظ فضای کاری تازه سازماندهی شده است. این میتواند شامل کارهای معمولی مانند پاک کردن، گردگیری و غیره یا انجام تعمیر و نگهداری ماشین آلات، ابزارها و سایر تجهیزات باشد.
- استانداردسازی (seiketsu): مجموعه ای از استانداردها را هم برای سازمان و هم برای فرآیندها ایجاد کنید. در اصل، اینجا جایی است که شما سه S اول را میگیرید و قوانینی را برای چگونگی و زمان انجام این وظایف تعیین میکنید. این استانداردها میتوانند شامل برنامهها، نمودارها، فهرستها و غیره باشند..
- حفظ کردن (shitsuke): شیوههای جدید را حفظ کنید و برای حفظ نظم و انضباط ممیزی انجام دهید. این بدان معناست که چهار S قبلی باید در طول زمان ادامه یابد. این امر با ایجاد حس انضباط شخصی در کارکنانی که در 5S شرکت خواهند کرد به دست میآید.
5S چگونه کمک میکند؟
5S اتلافهایی را که ناشی از یک منطقه کاری نامناسب است (مثلاً اتلاف وقت به دنبال ابزار) را حذف میکند.
مزایای 5S
مزایایی که از اجرای یک برنامه ناب 5S حاصل میشود عبارتند از:
- بهبود ایمنی
- در دسترس تر بودن تجهیزات
- نرخ نقص پایین تر
- کاهش هزینهها
- افزایش چابکی و انعطاف تولید
- بهبود روحیه کارکنان
- استفاده بهتر از دارایی
- تصویر سازمانی بهبود یافته برای مشتریان، تامین کنندگان، کارکنان و مدیریت
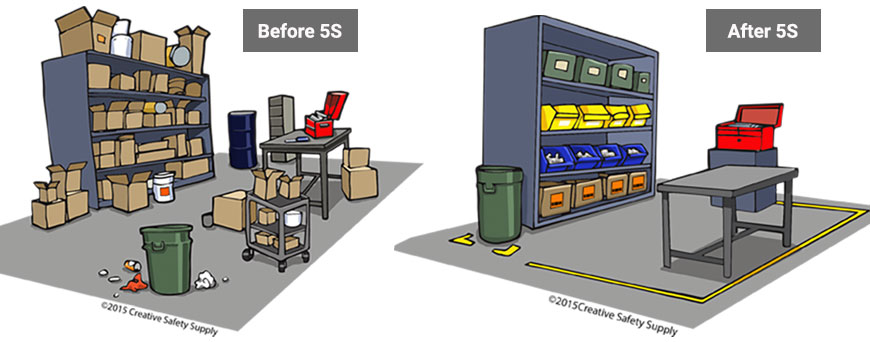
۲۵- برنامه، اجرا، بررسی، اقدام ( PDCA)
PDCA چیست؟
PDCA مخفف Plan-Do-Check-Act است و یک روش چهار مرحلهای برای ایجاد و انجام تغییرات است. روش PDCA یک چرخه است و بارها و بارها تکرار میشود تا به بهبود مستمر منجر شود.
PDCA پایه و اساس بهبود مستمر یا کایزن است. رهبران اهداف (برنامه ریزی) را بر اساس یک مبنا از عملکرد تعیین میکنند. تیمها برای دستیابی به اهداف، بهبودهایی (Do) را اجرا میکنند. سپس آنها تغییر را برای ارزیابی عملکرد در برابر هدف اندازه گیری میکنند (بررسی). اگر تیم به سود قابل اندازه گیری دست یافته باشد، با به روز رسانی کار استاندارد شده، روش جدید را استاندارد (Act) میکنند. این تضمین میکند که بهبود پایدار است.
چرخه PDCA یک چارچوب ساده اما قدرتمند برای رفع مشکلات در هر سطحی از سازمان شما است. این میتواند بخشی از یک فرآیند برنامه ریزی بزرگتر باشد، مانند هوشین کانری . رویکرد تکراری به تیمها کمک میکند تا راه حلها را بیابند و آزمایش کنند و آنها را از طریق چرخه کاهش اتلاف بهبود بخشند.
مراحل پیاده سازی
- برنامهریزی: برنامهریزی و نتایج مورد انتظار را ایجتعریفاد کنید. منطقهای را پیدا کنید که نیاز به بهبود دارد و برای تغییر برنامهریزی کنید
- انجام: اجرای برنامه. تغییر را در مقیاس کوچک آزمایش کنید
- بررسی: نتایج مورد انتظار به دست آمده را تأیید کنید. با تجزیه و تحلیل نتایج و تعیین آنچه یاد گرفته اید، نحوه انجام آزمون را بررسی کنید
- عمل: بررسی و ارزیابی؛ دوباره انجامش بده. ر اساس آنچه آموخته اید اقدام کنید. اگر تغییری که انجام دادید جواب نداد، از ابتدا شروع کنید و تست دیگری را تعیین کنید. از شکستهای خود استفاده کنید تا مشخص کنید بعد به کجا خواهید رفت.
زمان استفاده از چرخه PDCA
از چرخه PDCA زمانی استفاده کنید که:
- شروع یک پروژه بهبود جدید
- توسعه یک طراحی جدید یا بهبود یافته از یک فرآیند، محصول یا خدمات
- تعریف فرآیند کاری تکراری
- برنامهریزی جمعآوری و تجزیه و تحلیل دادهها به منظور تأیید و اولویتبندی مشکلات یا علل ریشهای
- اجرای هرگونه تغییر
- کار در جهت بهبود مستمر
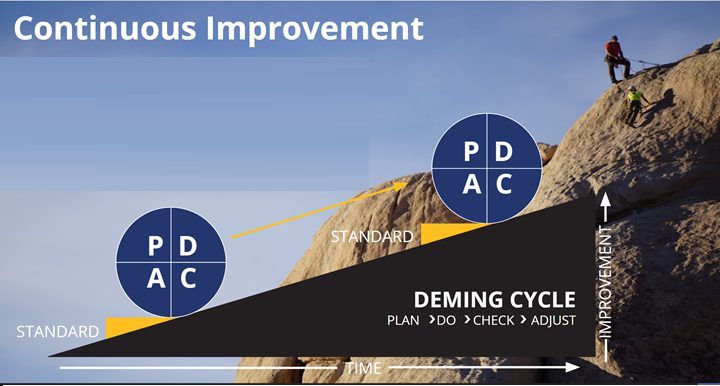
۲۶- کار استاندارد شده Standardized Work
کار استاندارد چیست؟
کار استاندارد ابزاری است که برای مستندسازی بهترین شیوههای فعلی، بهبود استاندارد، و اطمینان از اینکه استاندارد جدید به پایهای برای بهبود تبدیل میشود، استفاده میشود. یک استاندارد خوب تعریف میکند که چه کسی کار را انجام میدهد، چه زمانی آن را انجام میدهد و چگونه آن را انجام میدهد. کار استاندارد یک سند “زنده” است که به راحتی قابل تغییر باشد.
مستندسازی کار استاندارد باید در یک فرآیند مشارکتی افرادی که واقعاً درگیر کار هستند در کنار مهندسان و سرپرستان انجام میدهند. هنگامی که فرآیند استاندارد تکمیل یک کار به عنوان کار استاندارد شده مستند شد، فرآیند استاندارد باید به کارکنان (از جمله کارمندان جدید) آموزش داده شود و فرآیند باید در محل کار دنبال شود.
۳ عنصر کار استاندارد
کار استاندارد 3 جنبه مهم فرآیند تولید را بهبود میبخشد:
زمان تکت : نرخی که قطعات یا محصولات باید با آن تولید شوند تا بتوانند تقاضای مشتری را برآورده کنند.
توالی کار : مراحلی که اپراتورها باید در زمان تکت انجام دهند، به ترتیبی که باید تکمیل شوند.
موجودی استاندارد (یا موجودی در حین فرآیند): حداقل مقدار قطعات و مواد خام مورد نیاز برای اجرای عملیات.
مزایای کار استاندارد
- مستندسازی بهتر فرآیندهای جاری برای همه شیفتهای کاری
- آموزش آسان تر برای اپراتورهای جدید
- کاهش صدمات و فشارهای کاری.
- مبنایی برای بهبود مستمر.
- نظم و انضباط را به فرهنگ کاری میافزاید.
- کار تیمی را در سراسر سازمان افزایش میدهد.
کار استاندارد چگونه کمک میکند؟
کار استاندارد با بکارگیری مداوم بهترین شیوهها، ضایعات را حذف میکند. مبنایی برای فعالیتهای بهبود آتی تشکیل میدهد.
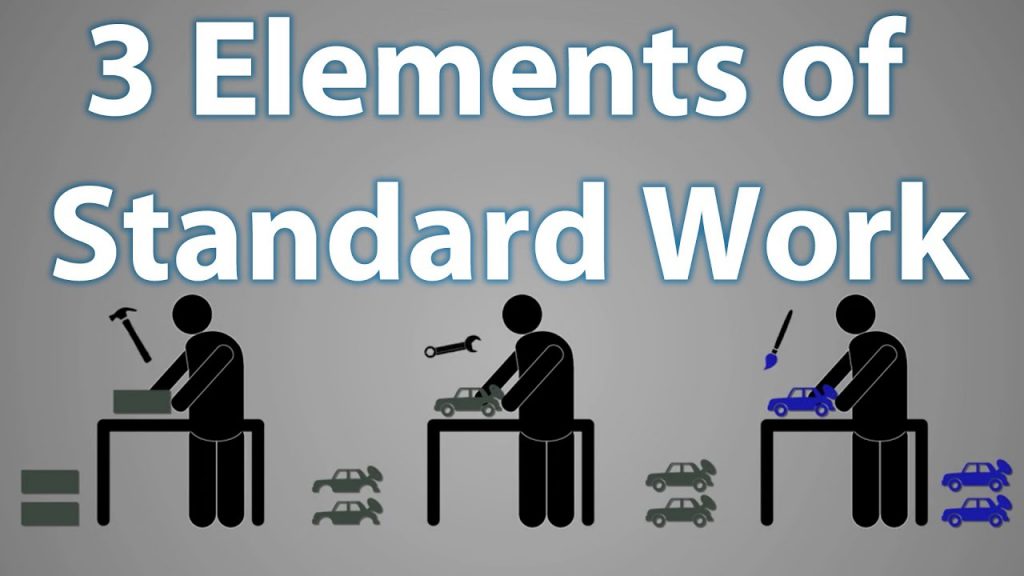
۲۷- آموزش حین کار
آموزش حین کار یک رویکرد عملی برای دستیابی و حفظ کار استاندارد است. این برنامه شامل یادگیری و تمرین عملی و یادگیری مهارتهای ضروری برای سرپرستان، رهبران تیم و هر کسی است که کار دیگران را هدایت میکند.
آموزش حین کار سابقه طولانی موفقیت در محیطهای صنعتی و تجاری دارد. این یک عنصر ضروری در برنامههای ناب و بهبود مستمر است. آموزش حین کار همکاری و روابط کاری مثبت را ایجاد میکند. این به سرپرستان، به سرعت و به روشی خوب آموزش کارکنان را آموزش میدهد. همچنین برای حل سریع و کارآمد مشکلات استفاده میشود.
امروزه از این اصول برای کاهش زمان آموزش و بهبود فرآیندهای تولید استفاده میشود. درازمدت، این فرآیند آموزشی برای ایجاد فرهنگ احترام، ارتباطات محکم و همکاری – برای نتایج نهایی طراحی شده است.. آموزش حین کار نحوه آموزش هر مرحله در فرآیند یادگیری و نحوه یادگیری هر مرحله را آموزش میدهد. برخی از مردم وقتی در مورد آن میشنوند به یک ضرب المثل قدیمی چینی فکر میکنند: «اگر به یک مرد ماهی بدهید، یک روز به او غذا دادهاید اما اگر به یک مرد ماهیگیری را بیاموزید تا یک عمر به او غذا دادهاید.»
اما واقعاً فراتر از آموزش «ماهیگیری» به یک نفر است. TWI اعتمادی را ایجاد میکند که روابط را ایجاد میکند. به سرپرستان زمان و منابع داده میشود تا به مربیان عالی تبدیل شوند.
مزایا
- ابزارهایی را که برای آموزش سریع و مداوم کارکنان جدید نیاز دارند، به کارشناسان و سرپرستان ارائه میدهد.
- به آموزش کارکنان موجود کمک میکند، بنابراین به جای اینکه سرپرستان صرفا ماهیگیری را به کارکنان آموزش دهند، کل نیروی کار یاد میگیرند که چگونه ماهیگیری را به طور موثرتر انجام دهند.
- بهترین راه را برای آموزش افراد خود و ایجاد استاندارد فرهنگ کاری جدید (چگونه همه با هم کار میکنند) است.
ارکان اموزش حین کار
روابط شغلی (JR):
روابط شغلی پایه و اساس روابط شغلی مثبت را به ما میآموزد. ایجاد و حفظ این روابط از بروز مشکلات جلوگیری میکند و در کسب وفاداری و همکاری دیگران غالب است.
روابط شغلی به سرپرستان میآموزد که چگونه روابط مثبتی با کارکنان ایجاد کنند و در عین حال همکاری و انگیزه را افزایش دهند. رفتار تیمی بیشتر را پرورش میدهد که در آن افراد با یکدیگر منصفانه و با احترام رفتار میکنند، و منجر به کارگرانی میشود که بیشتر به انجام درست کار اهمیت میدهند تا به روش خود .
آموزش شغلی(JI) :
آموزش شغلی به دنبال ایجاد ثبات از طریق اجرای پروتکلهای استاندارد است. این برنامه روش آموزش کارکنان در اجرای صحیح، ایمن و دقیق کارشان را آموزش میدهد. همانطور که اغلب اتفاق میافتد، اکثر فرآیندها توسط کارکنان مختلف با استفاده از روشهای مختلف انجام میشود. دستورالعمل شغلی مستلزم آن است که “بهترین راه” شناسایی شود و فرآیندها با این روش تطبیق داده شوند. اساس ثبات به این دلیل ایجاد میشود که هر شخص یک کار را به همان روشی که کارمند دیگری انجام میدهد انجام دهد.
روشهای شغلی (JM):
روشهای شغلی روشی اثباتشده برای حذف «اتلافها» از فرآیندها برای سرپرستان و اپراتورها فراهم میکند.
روشهای شغلی، افرادی را توسعه میدهد که میتوانند مشاغل خود را به بهترین شکل انجام دهند. تمام جزئیات هر شغل به شکل سیستماتیک مورد سوال قرار میگیرد تا ایدههایی برای بهبود ایجاد شود. با شناسایی و حذف اتلافها، استانداردها بهبود مییابند. همچنین میتوان وظایف را ترکیب کرد و وظایف را ساده کرد.
تمام اطلاعات موجود در SOP یا پروتکل بر اساس بهترین شیوههای شناخته شده تا آن لحظه است. کارکنان همیشه باید به دنبال فرصتهای بیشتر برای بهبود و بهینه سازی باشند. اگر کارمندی فکر میکند که راه بهتری برای انجام این فرآیند پیدا کرده است، باید این موضوع را با همکارانش در میان بگذارد. به عنوان یک تیم، آنها میتوانند تصمیم بگیرند که استاندارد را تنظیم کنند.
مزایا
- اغلب، مقرون به صرفه تر از سایر انواع روشهای آموزشی است.
- مربی خارجی لازم نیست.
- آموزش در طول شیفت کاری کارکنان انجام میشود.
- یک کارگر جدید این فرصت را دارد که با همکاران آشنا شود.
- می تواند بازخورد فوری در مورد عملکرد ارائه دهد.
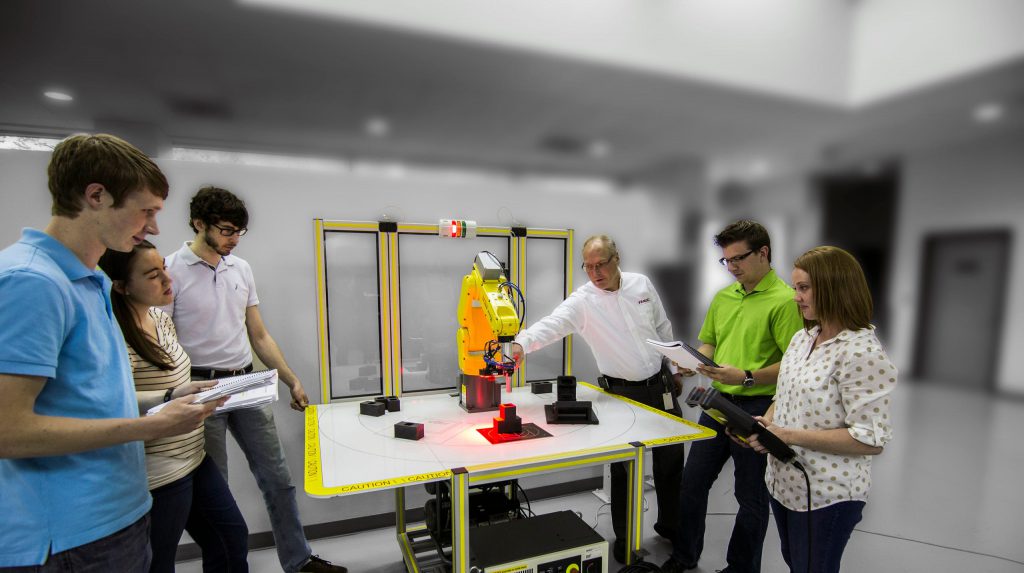
۲۸- اهداف هوشمند SMART Goals
اهداف SMART چیست؟
برای حرکت موفقیتآمیز به سمت تولید ناب ، داشتن یک برنامه جامع و اهداف روشن که باید برای آن هدف قرار گیرند، ضروری است. هنگام تعیین اهداف، مهم است که آنها واقع بینانه و مؤثر باشند. SMART مخفف – Specific, Measurable, Atainable, Relevant and Time- میباشد- که یک مسیر مطمئن برای ادامه مسیر در مراحل برنامه ریزی و اجرای بهبود کارخانه شما است. این را میتوان در هر مرحله از مدیریت زنجیره تامین اعمال کرد.
اهداف هوشمند روشی برای تعیین اهداف به شیوهای سازنده است. به منظور استفاده مؤثر از روشهای تولید ناب، مدیریت باید اهداف مناسبی را تعیین کند. در حالت ایده آل، آن اهداف باید به وضوح تعریف و ابلاغ شوند.
اهداف SMART عبارتند از: خاص، قابل اندازه گیری، قابل دستیابی، مرتبط و خاص زمان.
SMART مخفف چیست؟ هدف باید:
- مشخص – یک هدف باید عینی و مبتنی بر واقعیتها و ارقام واقعی باشد. به جای ایجاد اهداف گسترده مانند “بهبود مدیریت موجودی”، ایده را با گنجاندن جزئیات توضیح دهید.
- قابل اندازهگیری – نتایج باید با اعداد واضح تعیین شوند. زمانی که بتوانید پیشرفت را اندازه گیری کنید، تعیین اثربخشی استراتژی برای ارزیابی اجرا ممکن خواهد شد. پیتر دراکر گفت اگر نتوانید چیزی را اندازه گیری کنید نمی توانید آن را مدیریت کنید.
- قابل دستیابی – اهداف باید دست یافتنی باشند و خیلی جاه طلبانه نباشند. اهداف غیرممکن به روحیه کارکنان آسیب میزند.
- مرتبط – مشابه اهداف قابل دستیابی، اهداف باید به روشی واقع بینانه بر اساس منابع و زمان موجود تنظیم شوند. همانطور که کنترل جاه طلبی مهم است، باید مراقب تعیین اهداف غیرواقعی نیز باشید. حتی اگر میدانید که خرید همه تجهیزات جدید میتواند کارایی را به میزان قابل توجهی بهبود بخشد و ضایعات را کاهش دهد، به احتمال زیاد به دلیل محدودیتهای بودجه یا زمانی، انجام این کار ممکن نیست.
- چارچوب زمانی – برای تحقق اهداف باید یک چارچوبهای زمانی تعیین شود. زمان تعیین شده باید واقع بینانه بوده و قابل دستیابی باشد.
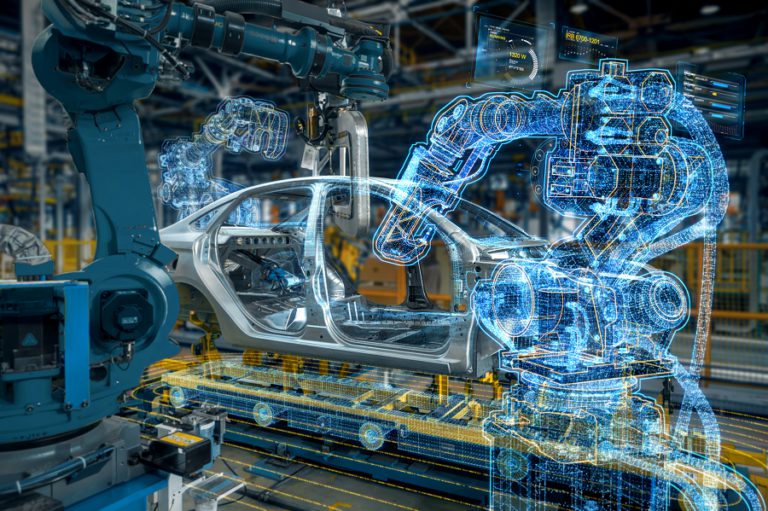
۲۹- شاخصهای کلیدی عملکرد Key Performance Metric
اگر موفقیت را نسنجید نمیدانید موفق هستید یا نه. اگر ایده روشنی از معیارهایی که موفقیت را توصیف میکنند داشته باشید، میتوانید پیشرفت را اندازهگیری کرده و فرآیند کار را برای دستیابی به نتیجه مطلوب بهبود بخشید. همانطور که پیتر دراکر گفت، “شما نمی توانید آنچه را که نمی توانید اندازه گیری کنید، مدیریت کنید.”
صرف نظر از صنعت، شما باید ایده روشنی در مورد چگونگی اندازه گیری موفقیت داشته باشید. شرکت شما باید چه نوع KPIهای ناب را ردیابی کند تا مطمئن شود همه بخشهای کسبوکار به خوبی کار میکنند. این KPIها به شما کمک میکنند تا مشکلات را در جریان کار شناسایی کنید، پتانسیل کامل یک تیم را کشف کنید و به بهبود مستمر برسید .
KPI چیست؟
KPIها معیارهایی هستند که برای ردیابی و تشویق پیشرفت به سمت اهداف حیاتی سازمان طراحی شده اند.
از KPIها برای مقایسه، تجزیه و تحلیل و بهینه سازی عملکرد عملیات کارخانه خود در طول زمان استفاده میکنند. چگونه عملکرد تولید را اندازه گیری میکنید؟ شاخصهای کلیدی عملکرد تولید، اندازه گیری کمی از نقاط قوت و ضعف را ارائه میدهد. KPIها بینشی را در مورد اینکه چگونه تولید به اهداف شرکت کمک میکند ارائه میدهد. مهم است که KPIهایی را با دقت انتخاب کنید که رفتار دلخواه را هدایت کنند.
برخی از KPIهای رایج تولیدی
- سرعت- اندازهگیری سرعت برای افزایش کارایی و سود ضروری است.
- تعداد تولید- این به مقدار محصول تولید شده اشاره دارد.
- نسبت مردودی- فرآیندهای تولید گاهی اوقات قراضه تولید میکنند. کاهش ضایعات برای افزایش بهرهوری ضروری است.
- زمان تکت- این میتواند به مدت زمان لازم برای تولید یک محصول یا مدت زمان لازم برای یک عملیات خاص اشاره داشته باشد. اندازهگیری این میتواند به شناسایی نقاط گلوگاه یا محدودیت در فرآیند تولید کمک کند.
- توقف ماشین – خرابی یا تعویض ماشین اغلب باعث خرابی میشود. j بهولید ناب دنبال کاهش زمان توقف تا حد ممکن است.
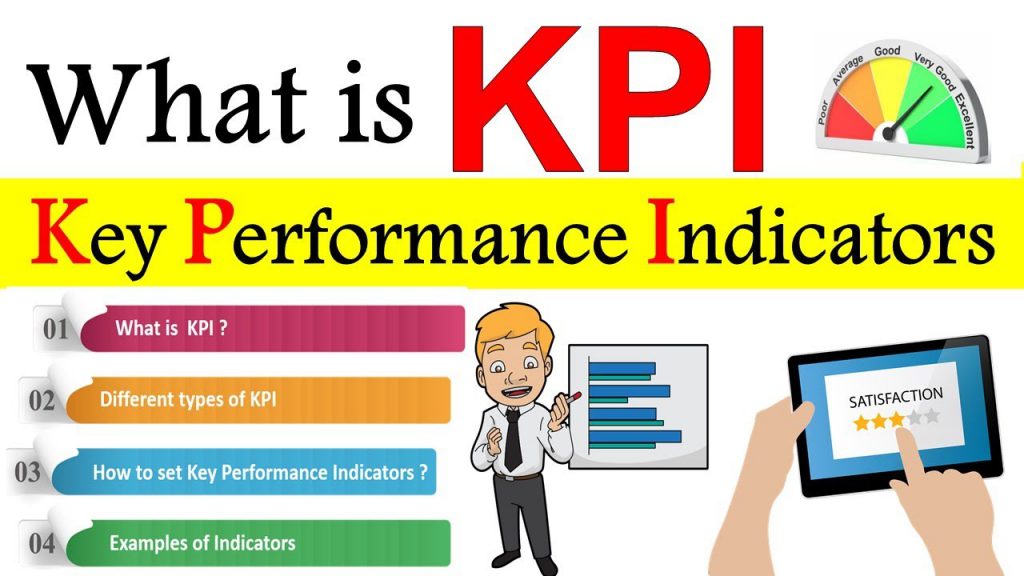